Tonnage
180
Matériel
Sable et Graviers
Production
0-4 mm, 0-8 mm, 4-8 mm, 8-22 mm, +22 mm
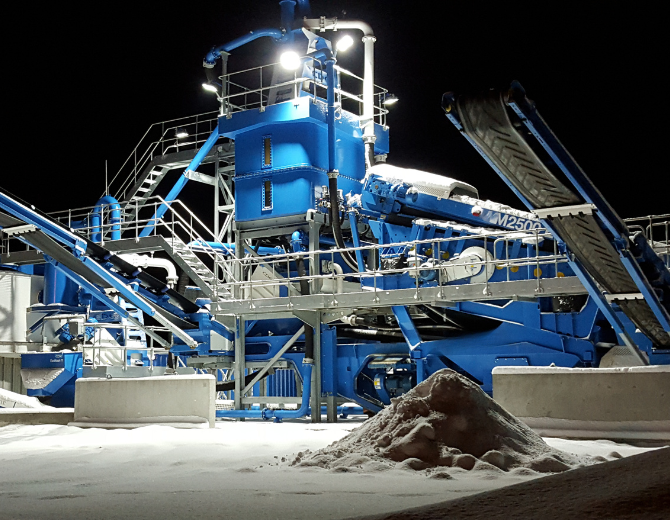
INTRODUCTION
En 2018, la société islandaise Steypustöðin acquierait deux entreprises, Alexander Ólafsson et Tak-Malbik, et avec elles, deux solutions de traitement par voie humide CDE mises en service en octobre 2016. Situées dans les carrières de Vatnskarðsnáman et Hólabrúarnáman en Islande, les deux usines de traitement ont été intégrées aux opérations de Steypustöðin, renforçant ainsi les capacités de traitement des matériaux de l'entreprise.
Les deux usines de traitement de sable et de graviers CDE d'origine comprenaient un M2500, une installation de lavage modulaire toute intégrée qui combine l'alimentation, le criblage, le lavage et le stockage sur un seul châssis compact et mobile, et un clarificateur AquaCycle pour la gestion et le recyclage de l'eau de process. Avec une capacité de traitement de 80 à 110 t/h (tonnes par heure) en fonction du matériau d'alimentation, l’installation produit 5 matériaux lavés : surdimensionnés à +22 mm, granulats en 8-22 mm et 4-8 mm, sable en 0-4 mm et 0-8 mm.
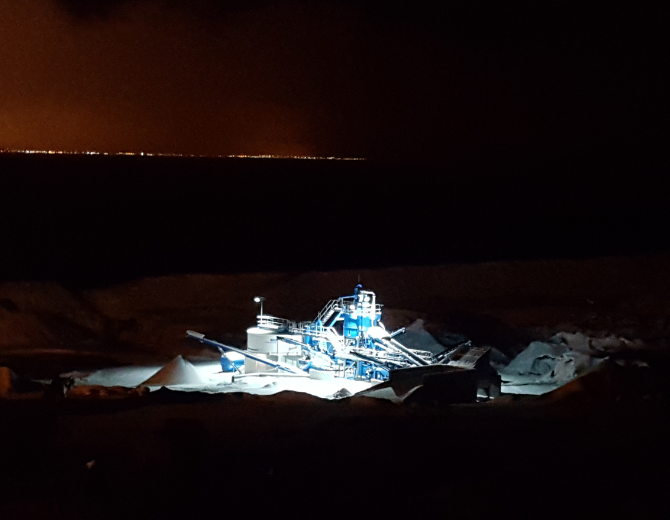
Problème
Confronté à une demande accrue de matériaux de construction de qualité supérieure, Steypustöðin n'était pas en mesure de répondre à la demande de l'industrie de la construction ou de constituer ses propres réserves de matériaux. Pour atteindre une production suffisante de matériaux sous-spécification, la capacité de l'usine devait être augmentée et Steypustöðin a décidé d'investir dans la modernisation de son usine CDE à Hólabrú.
La configuration originale de l'usine divisait les matériaux de 0 à 8 mm en deux fractions - 0 à 4 mm et 4 à 8 mm - sur l'étage inférieur du M2500. La pompe à jet, utilisée pour la fraction 4-8 mm, a été identifiée comme l'un des goulets d'étranglement, limitant le débit du matériau d'alimentation.
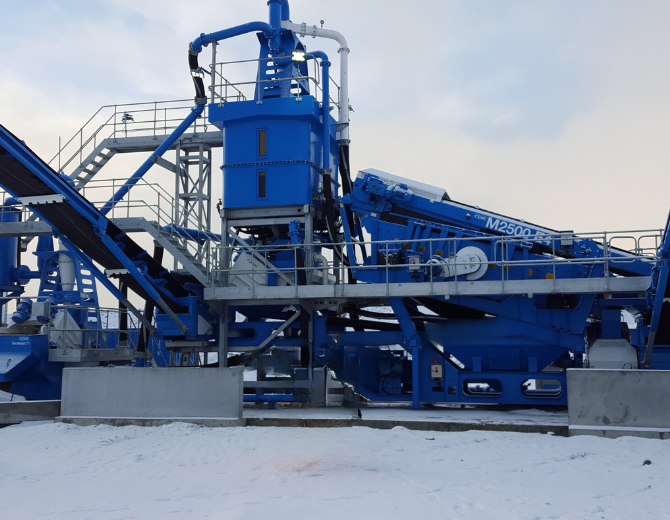
SOLUTION
En apportant des modifications minimes mais significatives à la conception initiale, nous avons été en mesure de multiplier par plus de deux la capacité de l'usine, dépassant ainsi les exigences du client.
Nous avons conçu une solution qui a considérablement transformé le fonctionnement et la performance de l’installation de Steypustöðin, tout en conservant son infrastructure de base et sa configuration d'origine. Cette solution comprend la suppression de la pompe à jet, remplacée par une nouvelle pompe traditionnelle, ainsi que l'utilisation complète de l'étage inférieur pour la fraction 0-8 mm, désormais pompée vers un nouveau crible d’essorage séparé où la fraction 4-8 mm est essorée, criblée et stockée via un nouveau système de convoyeur, tandis que le flux inférieur 0-4 mm du crible est pompé dans la configuration d'origine où il est déshydraté et où le matériau de moins 63 microns est éliminé par un nouveau cyclone de plus grande capacité.
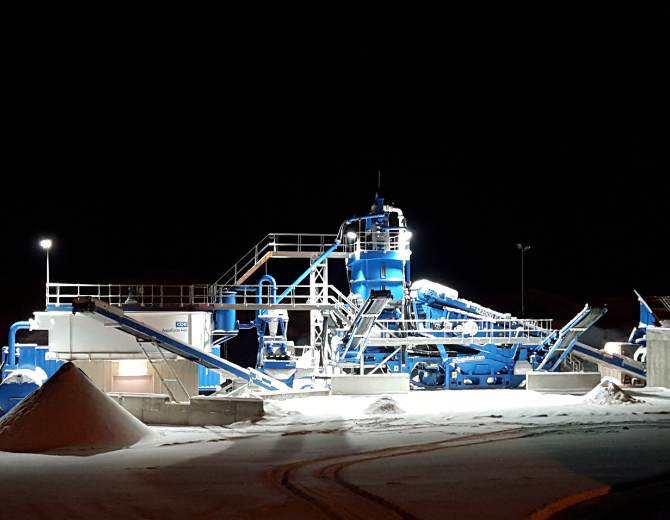
Résultat
L'usine fonctionne désormais à 180 t/h grâce à la modernisation qui a plus que doublé la production de sable et de gravier pour Steypustöðin, sur les fractions 0-4 mm et 4-8 mm, alors que l'usine continue à produire cinq matériaux.
Ce projet met en évidence la robustesse, la flexibilité et la fiabilité des nos technologies, renforcées par un service après-vente de premier plan, assuré par l'équipe CDE CustomCare. Nous avons développé une excellente relation de travail avec l'équipe de Steypustöðin et nous sommes ravis de contribuer au développement de l'un des principaux producteurs de béton en Islande.
Le client a été impressionné par le dynamisme et la détermination dont a fait preuve l'équipe CDE pour mettre au point une solution permettant d'augmenter la production de Steypustöðin en fonction de l'augmentation de la demande. La flexibilité de l’installation CDE et la capacité de nos experts à intégrer ces nouveaux composants dans l'opération existante plutôt qu’effectuer un changement complet ont permis une mise à niveau relativement peu coûteuse et ont eu un impact significatif sur la production, accélérant ainsi le retour sur investissement global.