Tonnage
150
Material
C&D Waste
Output
C33 Spec Concrete Sand, Fine Sand and 3 Washed Aggregates including a Pea Gravel
Turning dirt into dollars: CDE commissions waste recycling plant for Freehaven Materials
The 150tph plant in Long Island is transforming C&D waste into in-spec aggregates
On Long Island, construction waste has been a growing problem. With each new project, contractors are left with piles of excavation material and demolition debris – yet with landfill closures and rising disposals costs, getting rid of this waste has never been more expensive.
For Freehaven Materials, finding a solution to this problem meant staying competitive in a market where material costs were climbing, and landfill space was disappearing.
To gain a competitive advantage in full-scope heavy-civil projects, they wanted a solution that would turn waste into reusable materials and realized that wet washing could give them this advantage and generate additional revenue.
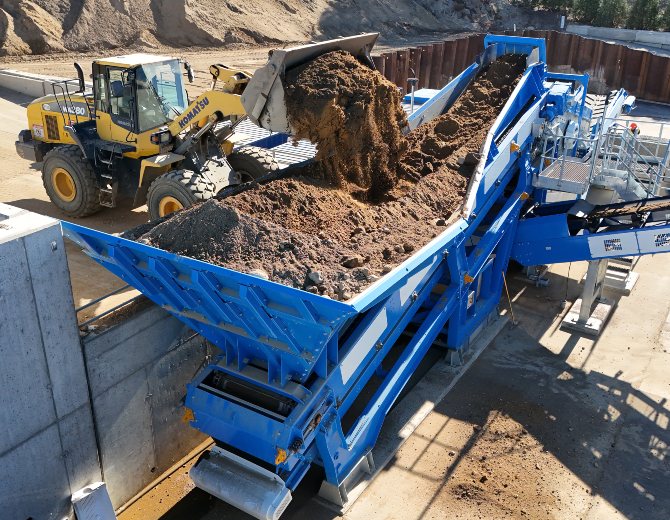
The Challenge
In 2023, Freehaven found its answer; a partnership with wet processing experts CDE and a cutting-edge 150tph wash plant installed right on its Brookhaven site. Suddenly, dirt was no longer an issue – dirt became dollars in the making.
Tom Hayes of Freehaven Materials remembers the turning point. “We were paying fortunes to dispose of perfectly good material, and it just didn’t make sense. With landfills closing and transport costs rising, we had to innovate to remain competitive. Partnering with CDE to install a wet processing plant allowed us to turn what was once waste into a valuable product. Now we’re recycling that material and putting it right back into local projects.”
Prior to this investment, Freehaven Materials had previously relied on dry crushing and screening, this partnership is its first venture in wet processing.
Creating materials for critical infrastructure
In early 2024, Freehaven commissioned a 150tph C&D waste recycling plant engineered by our expert team. Now, the Freehaven plant outputs a range of high-value products, including ASTM C33-spec concrete sand for high-strength mixes, a clean fine sand, and three grades of crushed stone ranging from pea gravel to larger aggregate.
These recycled aggregates are already finding their way into infrastructure projects across Long Island, including highways, bridges, and roads. Now instead of filing up landfills, it’s building the infrastructure needed to keep Long Island moving.
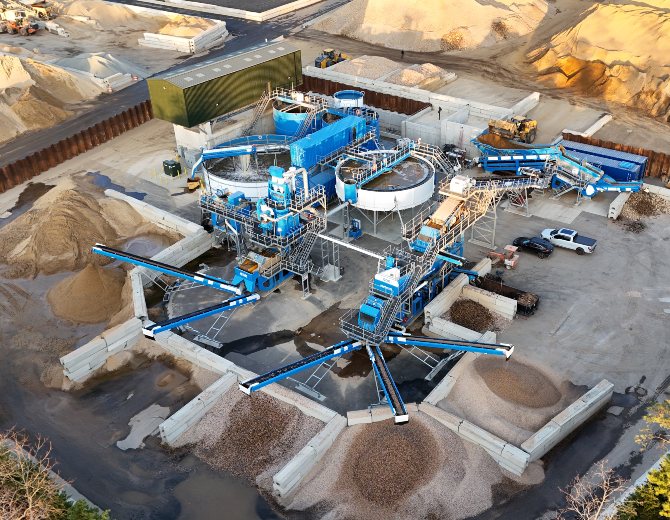
The Solution
The modular wet processing system incorporates an R4500 primary scalping screen, an AggMax™ scrubbing and classification system, an EvoWash™ sand washing system, a counter flow classification unit (CFCU) density and sizing classification system, an AquaCycle™ thickener for primary stage water management and an AquaStore water tank.
Working together, these technologies wash and sort mixed loads of excavation soil through a multi-stage process.
The innovative solution removes organics, cleans clay-bound materials, and scalps off overburden, ensuring that only high-quality material is recovered. The system then dewaters cleaned materials for use straight off the belts.
The AquaCycle and AquaStore integrated water recycling technology minimizes strain on local water sources by reducing the need for settling ponds, which in turn reduces the overall environmental impact of the plant.
Screens and classifiers then separate that material into specific gradations, producing sand and aggregates that are suitable for a variety of construction uses.
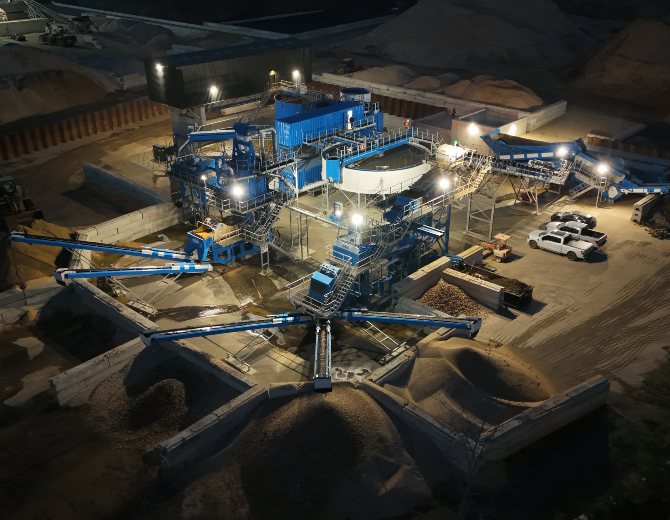
Optimal plant performance
The plant is also equipped with our innovative SmartTech application which enables customers to understand their plant’s performance, schedule maintenance and easily order parts.
Sensors fitted to across the plant provide up to 300 precise data points and continuously stream real-time, in-depth performance reports. Providing a full and transparent overview of the health of a plant, this live feed is accessible 24/7 through the SmartTech mobile app.
With this technology, Freehaven Materials can monitor feed rates, and results from SmartTech data showed that the plant consistently achieves an average feed of 171tph, exceeding the expected 150tph by 14%, resulting in 114% tph utilization.
SmartTech also shows that the Filter Press cycles times are very low with an average feed time of 13 minutes. Factoring in mechanical time, each cycle runs for approximately 28 minutes, allowing for higher material throughput and operational efficiency.
Challenge becomes opportunity
“There’s no shortage of construction waste on Long Island, and Freehaven recognized its potential,” says Joe Teahl, Business Development Manager at CDE. “By investing in this solution, Freehaven Materials not only reduced its own costs but also created a sustainable local supply of aggregates.”
Freehaven’s success demonstrates that with the right technology, a challenge can be turned into an opportunity. High disposal costs and virgin material scarcity aren’t problems unique to New York. They’re emerging all over North America, and especially in the greater metropolis area as landfills fill up and natural sand and aggregates dwindle – making it hard to source vital materials needed, particularly at a time when organizations are trying to minimize transportation and CO2 emissions.
Teahl points out the forward-thinking nature of this plant. “Freehaven is setting the example here. They’ve proven that recycled aggregates can meet industry needs without compromising on quality. It’s inspiring others in our industry to reconsider what’s possible with waste.”