Tonnage
180tph
Material
Sand & Gravel
Output
5 – 10mm, 10 – 20 mm & +20mm aggregates | coarse sand | fine sand
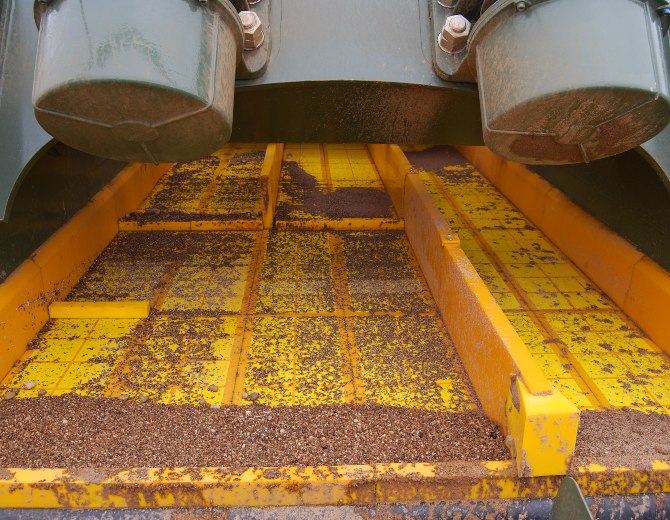
THE CHALLENGE
Lafarge and CDE have partnered on various projects, first working together in in 2004 on a project in Ireland.
The company’s Brooksby quarry is located near Melton Mowbray in Leicestershire opening for business in 2007. The company opened with a licence to extract 300,000 tonnes of sand and gravel and anticipated fifteen years production at the site. The site is being progressively restored as extraction progresses to become agricultural land and a complex of lakes. The sustainability agenda is one that Lafarge take very seriously, as can be seen by their membership of numerous wildlife trusts in the UK alone. While Lafarge are rightly recognised as one of the most prominent names in the global construction materials market, their work in the UK is characterised by a commitment to local community groups and initiatives.
Lafarge opened discussions with CDE about a new washing plant at Brooksby in late 2007 as a result of difficulties being experienced in processing the natural sand and gravel at the site.
"The presence of clay in the raw feed was proving to be a problem with our previous processing system and this was having a significant impact on the quality and commercial value of our final products,” says Andy Morris, Lafarge National Production Manager
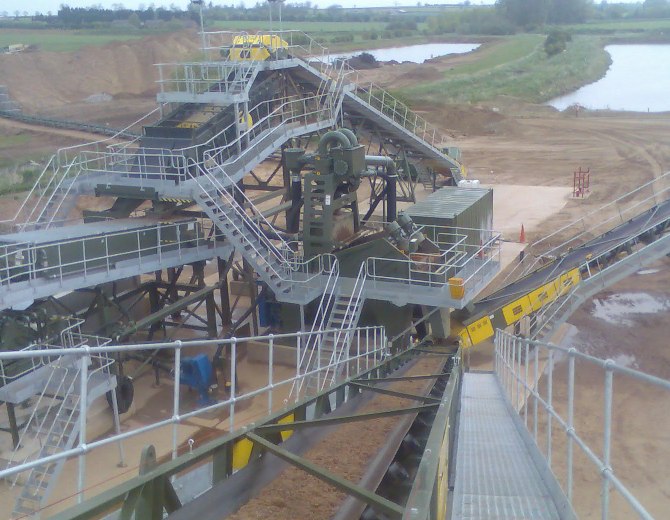
THE SOLUTION
The recommended solution which was installed and commissioned by CDE at the Brooksby quarry draws on a range of equipment from the CDE portfolio – hoppers, conveyors, ProGrade screens (both rinsing and dry sizing screens are included), an AggMaxTM attrition and classification system, and EvoWashTM sand plant.
Feed material is loaded into the hopper before transferring to the primary screening phase. Due to high levels of clay in the feed material the conveyor is fitted with scrapers to ensure the belts stay as clean as possible, minimising spillage and ultimately increasing plant efficiency.
At the primary screening stage a ProGrade double deck rinsing screen removes the oversize (+ 40 mm) material which is discharged into a concrete bay beneath the screen while the -5 mm material and slurry are sent to the EvoWash.
5 mm to 40 mm material is delivered directly to the AggMax system. This unit combines the RotoMax attrition system and ProGrade dewatering screens in a compact configuration that reduces space required on site to accommodate the plant. The RotoMax system tackles the level of clay in the feed material and is capable of handling up to 300 tph. Waste water from the RotoMax is sent to the EvoWash sand plant to recover any remaining -5 mm material. +5 mm material is delivered onto a dewatering screen before being sent to the dry sizing screen, which is a ProGrade D26 double deck screen. The dry sizing screen classifies products into 5 - 10 mm, 10 - 20 mm and +20 mm aggregates which are transferred to stockpiles by three 20 m static conveyors.
At the sand washing phase an EvoWash sand plant is employed and produces a coarse sand and a fine sand. The EvoWash’s deck is split to allow for dual sand production. The slurried waste water and -5 mm sand collected in the sump is pumped through the first of two 500 mm cyclones. Discharging onto the first side of the split screen with fine material falling to the sump with the waste water. The coarse sand is dewatered on a high frequency vibrating screen ensuring maximum dewatering.
The fine sand is pumped through the second of the 500 mm cyclones. The -63 micron material and waste water is removed via the cyclone overflow and sent to a ground sump for pumping to onsite lagoons. The fine sand is delivered to the second side of the split dewatering screen where it is dewatered to approximately 12% moisture content, ensuring it is ready for market straight from the belts.
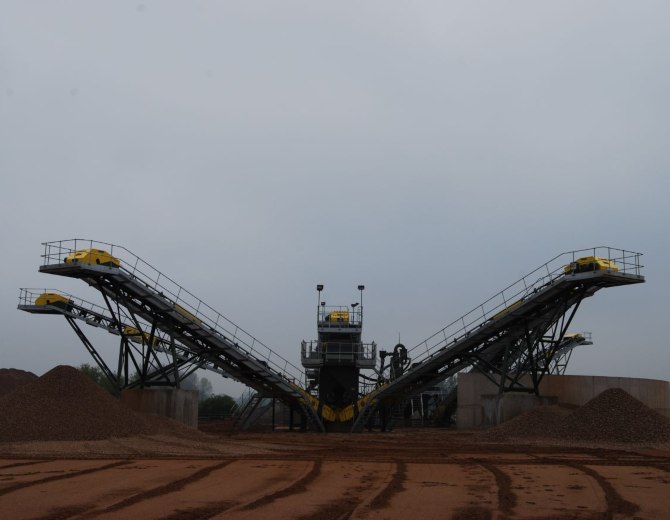
THE RESULTS
The CDE sand & gravel washing plant at Brooksby quarry has succeeded in addressing the specific issues identified by Lafarge as being critical to plant success. The system successfully deals with the clay content in the feed material to produce the high quality sand and aggregate products demanded by Lafarge to uphold their reputation as a leading supplier to the UK market. In addition to this, the superior dewatering of the sand product in particular allows Lafarge to quickly turn their products into revenue, delivering a fast return on its investment.