Tonnage
200tph
Material
C&D Waste, Excavation Waste, Hydro Excavation Waste, Non Hazardous Soils
Output
0-5mm Washed Sand | 5-20mm, 20-400mm & 40-800mm Washed Aggregates
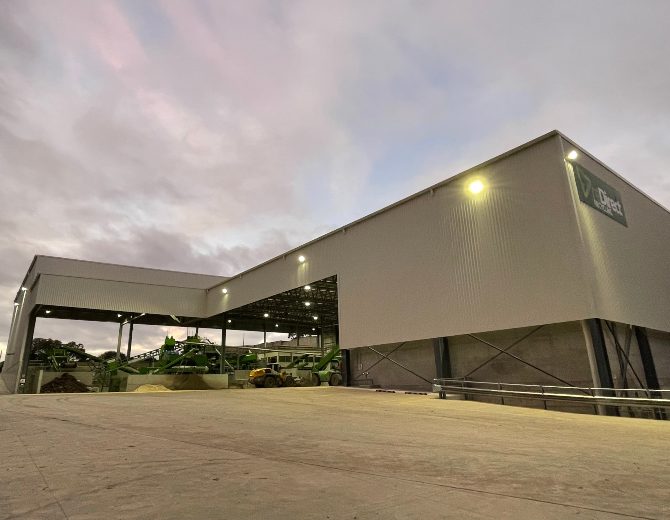
THE CHALLENGE
Part of the Borg group, reDirect Recycling offers efficient resource recovery management, creating an industrial ecology which diverts waste from landfill to return resources back into the economy. reDirect Recycling focuses on providing a disposal and recycling solution to customers generating construction, demolition and excavation (C,D&E) waste for both dry and wet materials.
Operating since 2020, reDirect Recycling manages one of New South Wales' largest hydro excavated mud recycling facilities, offering 24-hour service convenience for customers operating on large civil and infrastructure projects.
Bettergrow, part of the Borg group and sister company of reDirect Recycling, is a long-standing customer of CDE and currently operate a G:MAX dual stage wet recycling system for dewatering hydro-excavated muds and recovering a washed sand. Having previously worked with CDE, Bettergrow’s knowledge of the company’s extensive experience and in-country capability to service and support gave them the confidence to commission a second CDE solution.
CDE worked closely alongside reDirect Recycling to design and develop a plant that could handle both wet and dry materials to recover valuable resources and aid in landfill diversion.
Talking about the partnership with CDE, Neale Hogarth from reDirect Recycling said: “We knew that CDE was the right choice for us when we were embarking on this venture. They offer a wealth of experience and expertise in hydro-excavated muds, so it made complete sense.”
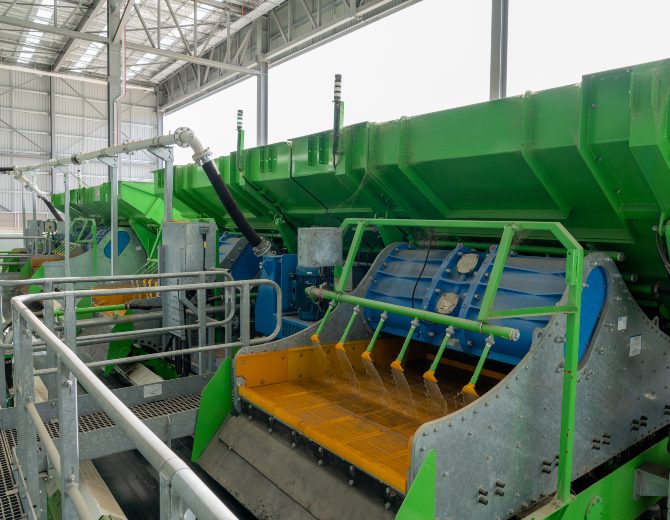
THE SOLUTION
CDE delivered a C,D&E waste recycling solution, as well as integrating four HYDRO:TIP units to process hydro-excavated muds.
The plant, which incorporates an EvoWash sand wash plant, AquaCycle A200 thickener with water tank, centrifuge decanter, R-Series Primary Scalping Screen, Infinity dewatering screens, and AggMax modular logwasher operates at a rate of 200tph.
The reDirect Recycling solution has two feed points, the R-Series and the four HYDRO:TIP systems. At the first feed point, solid waste material is loaded directly into the R2500 with a loader, while four trucks can simultaneously tip wet waste directly into the HYDRO:TIP bays at the second feed point.
The HYDRO:TIP™ is specifically designed to handle solid-liquid waste from hydro excavation tankers and street sweepers. It’s dedicated reception station ensures a safe platform to unload wet waste quickly and efficiently, without the need for an additional full-time operator to manually dredge and dewater material prior to feeding.
The R2500 screens the heavily claybound feed and removes any oversize material, thereby protecting downstream processes while also providing sufficient energy to break up and homogenise the feed. The material is then transferred from the R2500 to the AggMax on a conveyor where the overband magnet removes ferrous metal contamination.
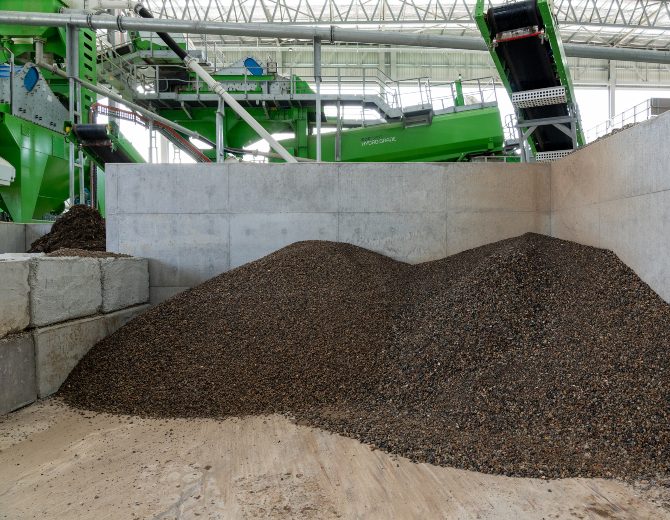
ENGINEERED FOR ZERO WASTE
At the AggMax, the upward flow classification function floats off organics onto the integrated trash screen for dewatering and stockpiling. The paddles of the RotoMax RX160 encourages aggregate on aggregate attrition scrubbing for breaking down clay conglomerates and liberating clean aggregate. The Infinity H2-60 screens and dewaters three aggregate products by size and any trace sand washed off is then processed in the EvoWash wash plant to recover a 0-5mm sand product.
Once the cyclone overflow (<75um clay and silts) has been treated and clarified in the AquaCycle, recyclable water overflows across the weirs and onto a static screen to remove lightweight contamination. The thickened sludge is conditioned and discharged from the AquaCycle clarifier to the sludge buffer tank and is then pumped to the centrifuge decanter for final dewatering. The recycled water from the AquaCycle and centrifuge is sent to the water tanks for recycling around the system.
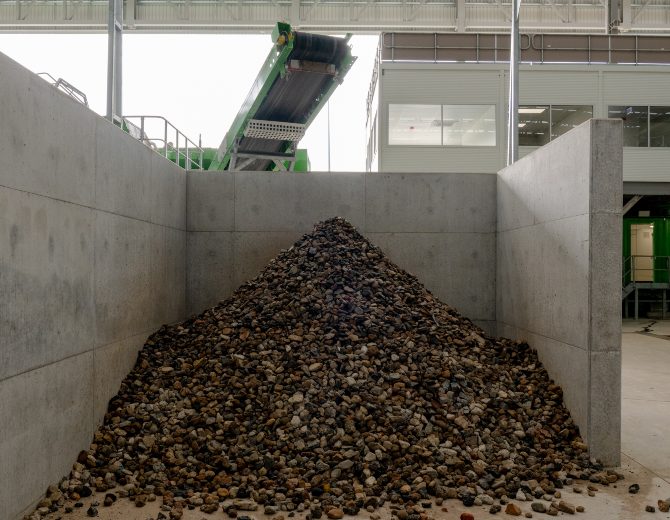
The Results
The state-of-the-art technology from CDE is allowing reDirect Recycling to produce a sand product (0-5mm) and three washed aggregates (5-20mm, 20-40mm and 40-80mm) as well as dewatered organics, clays and silts, to be repurposed in the construction market.
Neale Hogarth added: “It’s been a pleasure to work with CDE, the commissioning process went very smoothly, and the local team have been close at hand to support us through the journey with their expertise in dealing with highly variable dry and wet waste. We’re really looking forward to seeing how this plant can help in creating a circular economy.”
Riccardo Wong, CDE business development manager for Australasia, said that the new plant is allowing reDirect Recycling to close the loop on waste. “Both CDE and reDirect Recycling are passionate about sustainability and reducing waste going to landfill, so we used both of our expertise to create a solution which recovers and reuses valuable resources to be repurposed in the construction market.
“Plants like this are the future of the industry in their ability to minimise waste and maximise value. At CDE we’re passionate about enabling our customers with our innovative technologies so they can play their part in contributing to a circular economy.”