Tonnage
100tph
Material
Crushed Rock, Quarry By-Products
Output
Washed Sand & Aggregates
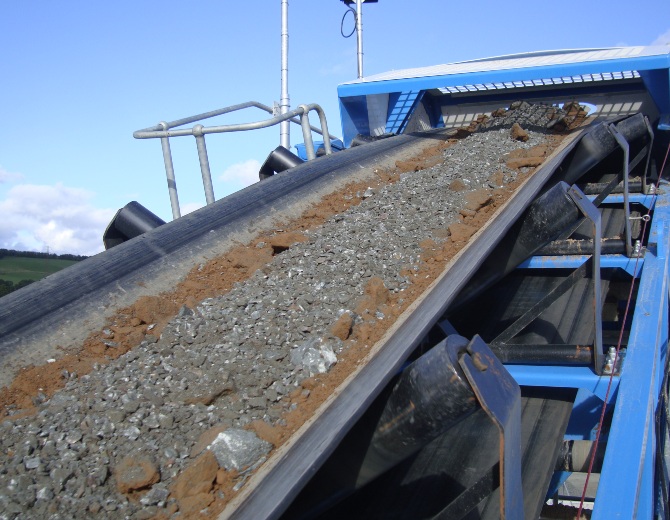
THE CHALLENGE
Skene Group was founded in June 1968. Originally involved in plant contracting, the company has diversified into being one of the UK’s leading independent operators in the construction supply sector.
For many years sand and gravel has been a major source of Scottish aggregates and in Skene Group’s early years natural sands and gravel provided the largest proportion of commercially produced aggregates in Scotland. Today, the market for sand and gravel in Central Scotland is thriving due to major infrastructural projects including the construction of the £1billion Forth road bridge, the new £500m Edinburgh Tramline connecting the City Centre to Edinburgh Airport and the overall increase in infrastructural investment.
The site of the CDE Washing Plant is Lomond Quarry, a hard rock quarry with a sand and gravel overburden, near Glenrothes, Fife in Scotland. The hard rock is a mixture of Whinstone and Dolerite and is notoriously hard to process.
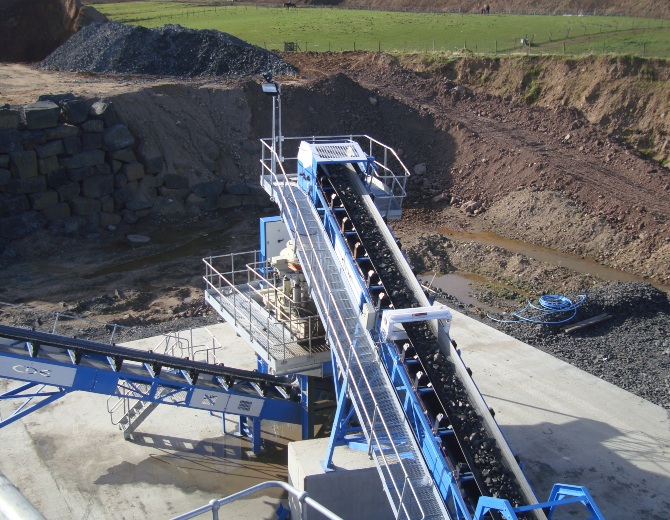
THE SOLUTION
Skene recognised that their existing washing plant on-site in Glenrothes required an upgrade. This led the company to speak to CDE about a new turnkey processing solution. Ideally, this solution would be a completely integrated package that would process material from crushing right through to producing clean washed products ready for sale and also for internal use.
It was always important to Donald Skene, Chairman of Skene Group, to ensure that the new solution would give Skene the ability to ‘blend’ natural sand, gravel and blasted rock in proportions to sustain the quarry.
“Central to our requirements for the washing plant was the blending of materials to ensure that our natural sand and gravel and hard rock could be mixed in usable proportions to manufacture concrete specification sand, therefore allowing us to sustain the quarry. Sustaining the quarry means we can retain and support our employees for the foreseeable future.”
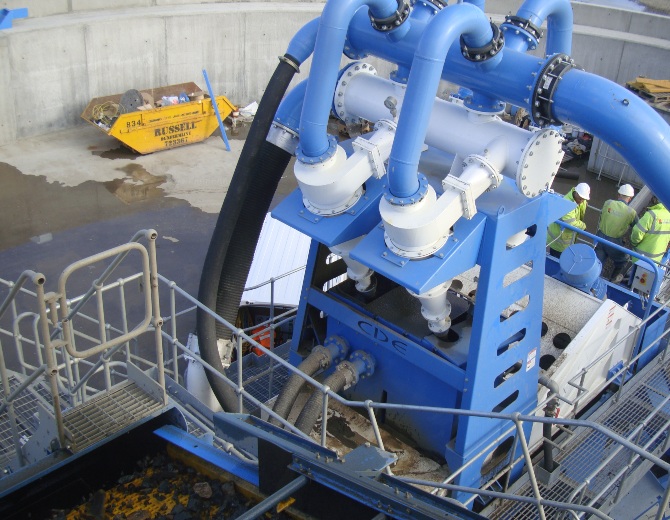
THE RESULTS
The CDE plant was installed and commissioned in Summer 2012. CDE produced an integrated solution combining both jaw and cone crushers with the washing plant.
The process begins with a blend of the naturally occurring sand & gravel overburden being fed to the plant via the L55 feed hopper. The feed hopper includes a tipping grid with 250mm spacings and an integrated belt feeder to ensure the efficient transition of material to the next stage of material processing. The feed conveyor delivers the material to a grizzly screen with the +60mm material going forward to a Jaw crusher.
Donald Skene commented on the superior design of the CDE plant, ‘In certain areas of the quarry the material is dirty, but the combination of the CDE sand plant and the AquaCycle thickener is so effective that it is hard to believe how dirty the raw feed is. The nature of the material being processed has changed since the previous plant was installed and this could have meant more water was required to run the new plant, but the AquaCycle solves this problem and ensures water is constantly recycled around the plant’.