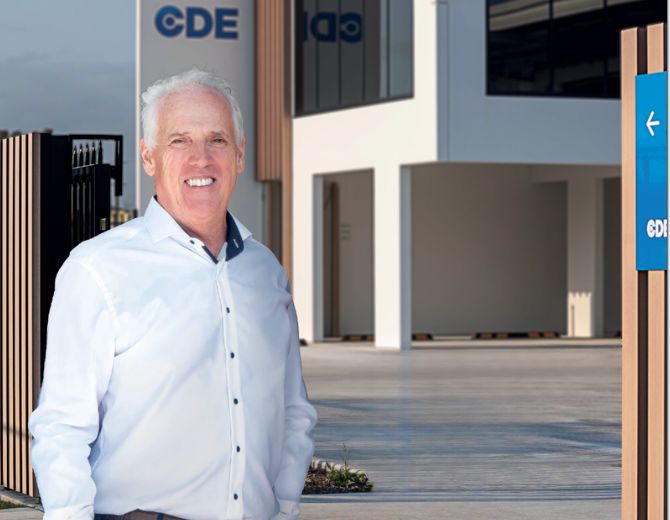
FEATURED IN WASTE MANAGEMENT REVIEW'S NOVEMBER EDITION
When CDE sold a sand and gravel washing system to WA Limestone in 2010, it set the seeds for an intercontinental commitment to do things right.
Fast forward 13 years and the Ireland-based processing equipment manufacturer has designed and engineered some of Australia’s largest resource recovery projects and been recognised with a slew of global awards.
In August 2023, CDE committed additional resources to the local market, officially opening new Australian headquarters in Queensland.
Tony Convery, CDE Executive Chairman and Founder, describes the office opening as a significant milestone in the company’s history.
“Our decision to establish a presence here was fuelled by our belief in the talent, innovation, purpose and passion that this country has to offer,” Tony says.
Together with customers, CDE is diverting millions of tons of material from landfill, protecting sands in areas where natural reserves are in decline, and enabling production to happen closer to markets.
Since its formation in 1992, the company has designed, manufactured, and commissioned wet processing plants around the world.
Its headquarters, in Cookstown, Northern Ireland, is home to a large campus dedicated to the wet processing industry. All the equipment is pre-wired, assembled and factory tested in manufacturing facilities in Cookstown and Monkstown, Northern Ireland.
The new 2900 square-metre Australian headquarters, based in Stapylton, near Brisbane and Gold Coast, is part of wider growth plans and follows the announcement and commissioning of several new large-scale projects in the Australasian market.
CDE has grown its local team to more than 20 experts across its business development, project management, installation, commissioning, and aftersales support teams, with plans for future recruitment under way.
More than 60 projects across Australia, New Zealand, and Papua New Guinea have been designed and engineered by CDE, including turnkey solutions for Repurpose It in Victoria – described as Australia’s most sophisticated resource recovery plant – and Walker Quarries – one of the newest and most advanced quarry wash plants in New South Wales.
In 2022, CDE was awarded the contract to design, supply and install a state-of-the-art washing solution for Rino Recycling for the treatment of construction and demolition (C&D) and commercial and industrial (C&I) waste materials at its Pinkenba site in Brisbane.
When operational, the new Rino Recycling plant will have the capacity to recycle more than 1.5 million tonnes of C&D waste material every year. It will also be able to recover recycled sand and aggregates, and supply the construction industry with a quality alternative to virgin quarried material.
Speaking at the CDE headquarters opening, Dan Blaser, General Manager, Rino Recycling, said the multi-million-dollar plant would take recycling to the next level.
It will increase Queensland’s 75 per cent recovery rate of C&D waste to 97 per cent and aims to produce aggregates that meet specifications for use in concrete. To that end, the plant includes a CDE EvoWash™, AquaCycle™ thickener to recycle up to 90 per cent of the process water for immediate re-use in the system, and filters.

Daniel Webber, CDE’s Australasian General Manager, says the company’s purpose is to create the best world possible, a ton at a time. To do this, CDE needs to be supporting its customers to realise their purpose and vision.
“Support means being there, when they need us,” he says, “and that means having CDE boots on the ground.
“We have great confidence in the potential of this market, and we’re committed to supporting new and existing customers, whose trust in CDE is key to making this investment in Australia possible. Our very first customers helped us to put the stake in the ground, which means companies like Rino now have this new facility to lean on as they move forward.”
CDE’s investment in its new Australian headquarters includes the development of fully stocked and managed stores to house high-wear, consumable and critical plant components.
Peter Neely, CDE’s CustomCare Regional Manager for Australasia, says that for the first time in the local market CDE can offer readily available parts.
“Responsive on-the-ground support and locally available parts with short lead times means we are better equipped to strengthen our direct relationships with customers, ensuring their plants continue to run material at optimum efficiency to support a fast return on investment,” Peter says.
The company’s pre-emptive approach to plant maintenance means thousands of replacement parts are readily available for immediate dispatch to customers throughout Australasia.
The headquarters launch was also an opportunity to showcase CDE’s technology including a plant management app, CDE SmartTech, and CustomCare Parts portal.
CDE SmartTech performance is standard with any CDE plant and provides performance insights to help customers understand their plant’s performance and schedule maintenance. Sensors on the plant continuously stream real-time data accessible 24/7 from anywhere in the world.
The portal will provide a 3D image of customer plants that can be used to identify parts, check their lifespans, get quotes and place orders. The portal has been rolled out to some customers with a view to make it available to all.
Daniel says CDE’s approach to aftercare is designed to ensure customers get the maximum performance from their equipment. Central to this is having a direct relationship with customers and continuing to invest resources in the markets where they are based.
“Our investment in Australia is but one part of wider plans to invest in and resource our regional teams and offices to provide the best level of care possible to protect our customers’ investments,” he says.
Tony agrees the office represents more than just walls and desks. It’s a commitment to continuing to forge connections with the local community and partners.
“Anybody that’s been to our office knows that every day, in everything we do, we strive to do it right and be the best. To do what’s practical so that our people can have a vision and really understand that the customer wants top level design, top level delivery, top level equipment, and then – and that’s what this headquarters is all about – top level back-up.
“The responsibility to do things right is something that’s very close to my heart, in terms of setting up efficient, eco-friendly facilities, whether they’re recycling water or waste materials. And it’s something that I know is deep in every Australian’s heart.
“I think together we can create a legacy that will inspire generations to come, will end this futile cycle of waste and make the world a better place.”