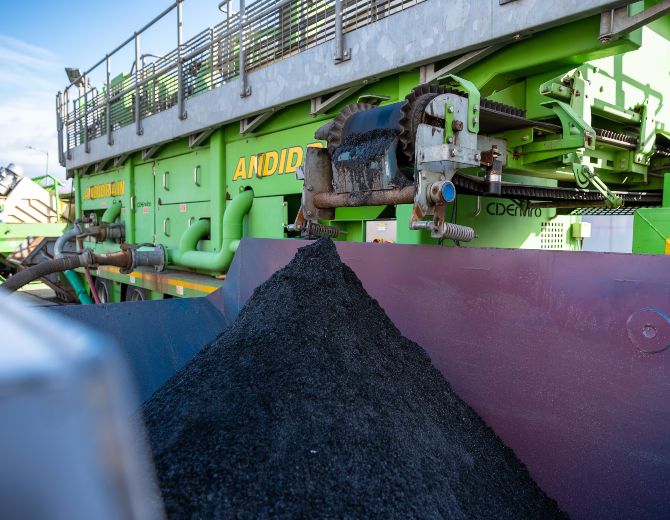
Reduce Waste to Landfill
We have been delivering wet processing systems for 30 years and have more than 2,000 systems in operation worldwide.
With a sole focus on wet processing, we have earned a reputation globally for delivering game-changing solutions that empower customers to maximise their natural resources. The range of wastewater processing plants includes the MSU:10, S:MAX, G:MAX and the D:MAX.
Mark Malone, our Business Development Manager in Australia, explains how the D:MAX technology ensures maximum solids removal and dewatering of waste across a variety of troublesome waste streams in a highly mobile, trailer-mounted configuration.
“The use of the D:MAX has a huge impact on the volumes of waste sent to landfill, it also means that the material that must go to landfill is safer and easier to handle and assists in protecting our water infrastructure.”
The D:MAX units are designed to remove contaminants such as Rag, a generic term for the fibre, paper and plastic-based materials, and Grit, a generic term for sand silt and stone material, that enter wastewater treatment from domestic, industrial, and urban sources. They use high frequency vibrating screen and hydrocyclone technology to separate both rag and grit contaminants from the wastewater.
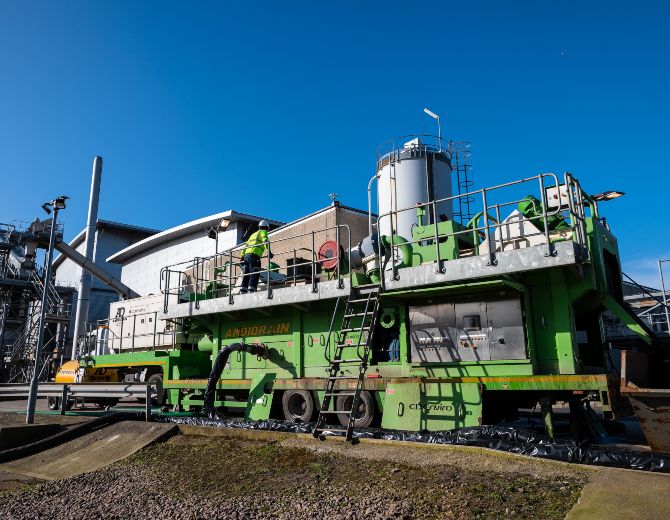
On The Move
The D:MAX is a mobile, trailer-mounted, multi-stage separation and recycling solution used to process a variety of materials from the water and wastewater treatment process.
The contaminated wastewater is delivered to the D:MAX by means of a pump or by bucket via the onboard hopper and fed directly onto the first of two onboard high frequency vibrating screens.
Mark says this first screen is typically fitted with six-millimetre aperture media. It separates the rag material as well as dewaters it and then discharges it directly at the end of the screen, typically into a collection bin.
The wastewater that passes through the first screen reports to a collection sump prior to being pumped to a specially configured hydrocyclone that diverts any remaining solids/grit material from the wastewater and onto the second of the high frequency vibrating screens.
The vibrating screen catches and dewaters this finer material before it too is discharged into a collection bin.
“Depending on the application, these discharged materials can be rinsed prior to being dewatered and collected as recyclable material in whatever grade is determined by the mesh size used in the screens,” Mark says.
Mark says the D:MAX plant features an ADR compliant trailer, is self-powered with an on-board generator, and incudes CDE hydrocyclone technology, CDE Infinity high frequency dewatering screens, a telescopic product conveyor, a modular, non-bolted, polyurethane screen media in both screens, efficient vibrating motors and an on-board panel.
The D:MAX has been successfully used by wastewater maintenance and drain cleaning contractors, and water utility providers for de-gritting of raw sewage; feeding screening and de gritting of tank/digester clean outs, etc and de-gritting of lagoon sludge prior to digesters.
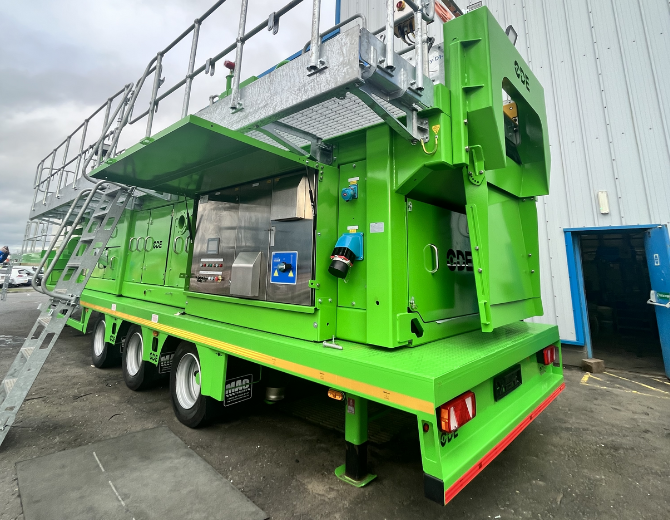
Benefits To The Max
Mark says reduced operations costs are just one of benefits for companies using the D:MAX.
“Carbon footprint and transport costs are reduced because the D:MAX can be easily moved around several sites if required, facilitating processing in-situ at a variety of locations. This minimises the transport movements required to bring waste material to a processing site and recovers 80 per cent of grit, meaning less waste to dispose of,” he says.
“Operations are accelerated by separating waste solids from liquid on site rather than transporting all waste off site.”
Mark says reduced solids passing through pumps, tanks and cyclones reduces wear and, as a consequence, the requirement for unnecessary maintenance. Grit, sand, and plastics are removed in the pre-treatment stage, maintaining capacity in tanks further down the treatment line for biomass power generation.
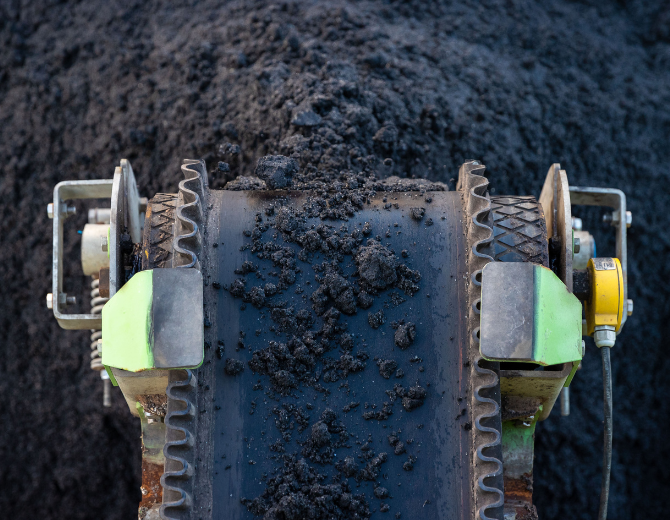
Return On Investment
The D:MAX produces a dewatered grit product suitable for a variety of further applications. This material can represent up to 90 per cent of the total waste. Mark says recovery of this material alone has a huge impact on the volumes of waste to be sent to landfill.
Mark describes the D:MAX as adaptable and easy to operate.
He says variable speed drives conserve energy and ensure the D:MAX system can adapt to accommodate surges of rag or grit and variation in feed material. It also comes equipped with its own onboard generator for ease of operation; providing additional flexibility on site to run ancillary equipment.
The telescopic product conveyor, which can be deployed on either side of the D:MAX, gives the D:MAX an added degree of flexibility to cope with the individual requirements of the site it is operating on.
Other features include standard compliant walkways to ensure quick, easy, and safe access for maintenance. The walkways and safety lights retract for transport.
We have an extensive network across Australasia of engineering and support professionals. They provide maintenance and technical support to customers operating the D:MAX and all other products within our portfolio