Tonnage
400
Material
Dredged Sands, Sand & Gravel
Output
0-2mm & 0-4mm Sand and 4-10mm & 10-20mm Aggregates
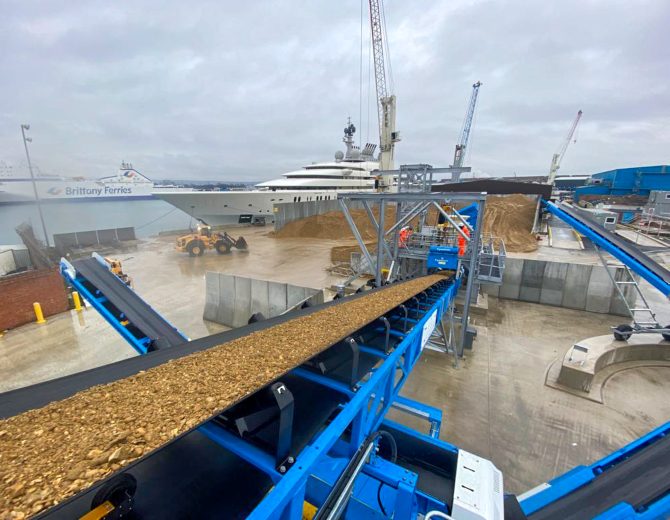
The Challenge
New 400tph marine dredged sand wash plant installed in Portsmouth for Brett Aggregates.
With history dating back over 115 years, Brett is a building materials group comprising of seven companies, providing aggregates, concrete and paving products to commercial and domestic markets.
As one of the UK’s leading independent aggregate producers, Brett Aggregates has over 60 locations across the South East of England and sells around six million tonnes of aggregate sales per year.
Commenting on the two companies’ working relationship William Melanophy, Head of Business Development UK & Ireland at CDE said: “We have been working with Brett Aggregates since 2018 having worked together on other sites. With this pre-existing relationship, we’ve been able to showcase our innovation, and the team at Brett Aggregates has seen our technologies in action, so they knew we could deliver the right solution.”
Ben Johnson, Production Manager for Brett Aggregates added: “This is my first time seeing a CDE plant be installed from the ground up. The install was well organised and completed in good time. The compact size and the efficiency of the plant really adds value to our operation, allowing us to maximise storage on site.”
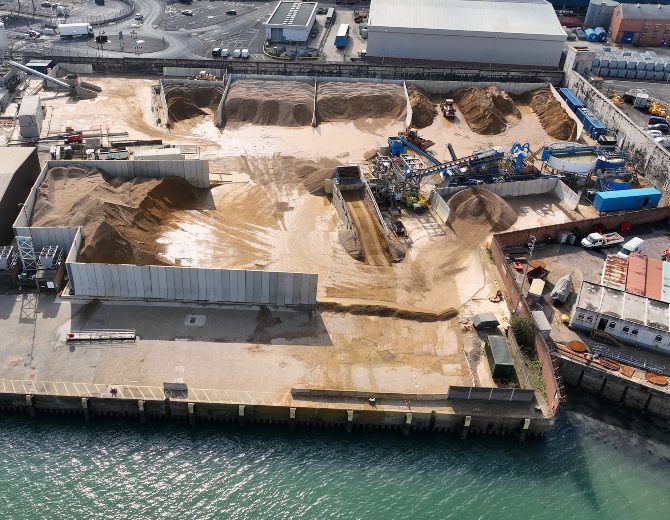
The CDE Solution
One of the biggest challenges with this plant was the limited space. The site is in close proximity to a Royal Navy base, and planning permissions allowed for a low-level plant. With the limited space available, we designed and commissioned a 400tph modular sand wash plant with a compact footprint in order to meet Brett Aggregates’ needs.
To process the marine dredged material, we engineered a solution which comprises of the M-Series modular wash plant with integrated hopper, a triple deck of Infinity inclined screens, an EvoWash™ sand washing system, and AquaCycle™ thickener for primary stage water management and an AquaStore water tank.
With Brett Aggregates seeking a plant with a minimised footprint, we provided an AquaCycle and AquaStore to this solution, both of which work in unison to remove the need for settling ponds, which was imperative for Brett Aggregates due to the limited site capacity. The AquaCycle thickener is a single compact highly efficient water management solution that minimises costly water consumption by ensuring up to 90% of the process water is recycled for immediate recirculation. The AquaStore receives recycled water from the AquaCycle which is then recirculated, reducing the volume of fresh water required to feed your washing plant.
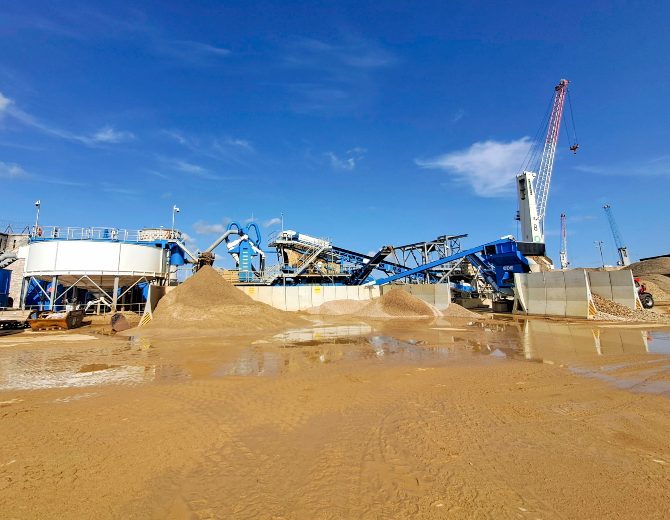
Engineered For Maximum Performance
Another mechanism to maximise performance in the limited space, was using a sludge re-blend system. This is product that is put back into the sand as typically marine dredged product is less than 3% silt. This allows Brett Aggregates to control the flow back into the buffer tank and supports the production of high-quality sand products to be produced on site.
As well as this, our M4500 modular wash plant integrates feeding, screening, sand and aggregate washing and stockpiling on a single chassis. The M4500 also incorporates a VibroSync drive system on the integrated Infinity dewatering screen which ensures even distribution of material across the full screening area for efficient dewatering of material.
Adding to this, our design team incorporated an EvoWash sand washing system. A compact and modular solution, the EvoWash separates the smaller sand and gravel fractions through an integrated high-frequency dewatering screen, sump and hydrocyclones which provide unrivalled control of silt cut points and eliminates the loss of quality fines with significant commercial value.
Within this solution we also installed our OptiMax technology which constantly reads live material data in the washing process to monitor the plant’s performance so that any necessary enhancements can be made.
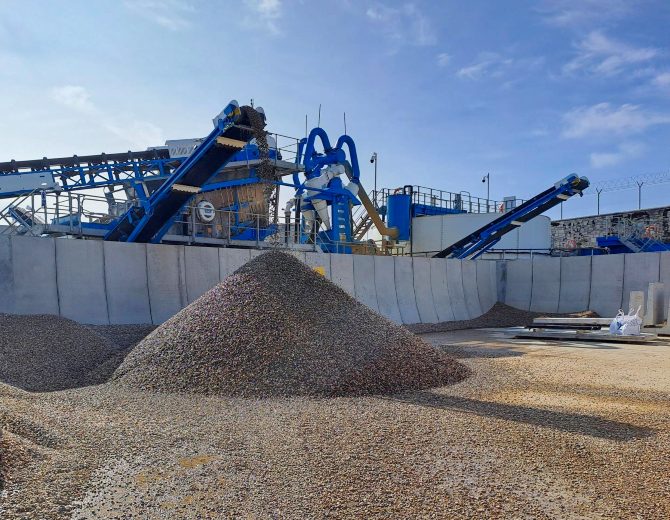
The Results
The solution enables Brett Aggregates to produce two sand products, a 0-2mm, 0-4mm, and two aggregate products, 4-10mm and 10-20mm, which will be used for concrete production.
Thanks to investment with CDE, Brett Aggregates has capitalised on an opportunity to build a successful wharf processing site in Portsmouth which has opened many opportunities within the area and increased business.
Ben Johnson added: “It’s been great working with CDE on this project. The maintenance of the plant is straightforward and the aftercare support has been good. The processing, maintenance and running of the plant have been consistent since commissioning in early 2024. The team at CDE have been really engaged with us from the start of the process, updating us on the designs, deliveries and installation milestones, right through to today to ensure the plant is still running as efficiently as possible.”