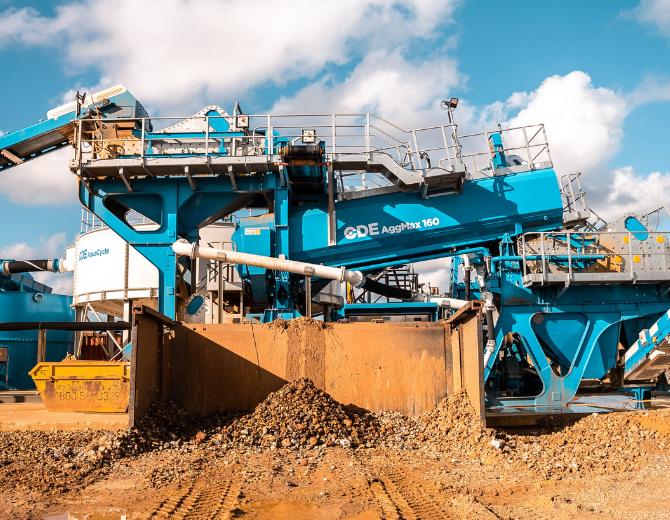
From Single Tipper to Industry Leader
It is over 40 years since the Mick George Group started trading with just a single tipper lorry. Fast forward those 40 years and the name is synonymous with a wide range of construction-based services across the region.
Now operating over 600 HGV vehicles from over 40 separate sites, employing in excess of 1,000 local people, gives an indication of the scale to which the business has evolved over the years and explains why they have grown to become one of the leading suppliers to the construction industry in the heart of East Anglia and East Midlands.
From their humble beginnings with a single truck the group has expanded massively to include specialist bulk excavation and earthmoving services, demolition and environmental management, a wide range of skip hire and waste management services and aggregate and concrete supply. With expansion into these sectors also came geographical expansion allowing services to be delivered across a wider area, yet still with a local feel. Such expansion has brought the company into operating landfill sites, waste transfer stations and quarries all aimed at offering bespoke, cost-effective solutions to commercial, trade and residential customers.
One of the largest sectors the company works in is the supply of aggregates supplied from both their own quarries and also recycled from material recovered from skip and tipper waste.
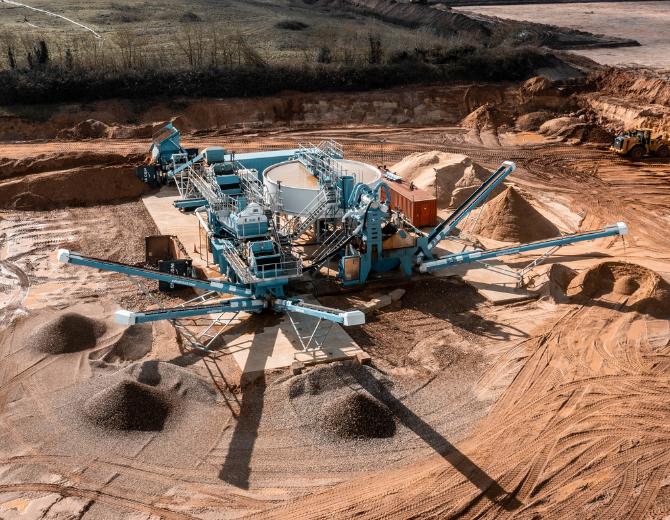
A Strategic Investment
As the Group have done ever since they started, quality is the name of the game, and this is mirrored in the supply of aggregates. The company’s Mayton Wood quarry near Norwich produces a range of sand and gravel products sold both to a variety of external customers and also used within the company’s own concrete batching plants.
To effectively clean and process the excavated material, Mick George has invested in a new state-of-the-art wash plant from CDE which was supplied through our strategic partner in the UK, Molson Washing.
“We required a plant that would not only give us the capacity to wash a large volume of material on an hourly basis, but we also wanted it to be reliable, easy to work with and environmentally friendly too.” Mark Shackcloth, Site Manager for Mayton Wood commented.
There are several manufacturers offering bespoke washing plant solutions to the UK market and following detailed discussions with many of the leading brands, the Mick George team sat down with Molson Washing, part of the Molson Group, to discuss their options. “We liked what Molson put across to us. Their proposal was very detailed and thorough, it put us at ease knowing they were exactly on our train of thought when it came to meeting our requirements.” Mark commented.
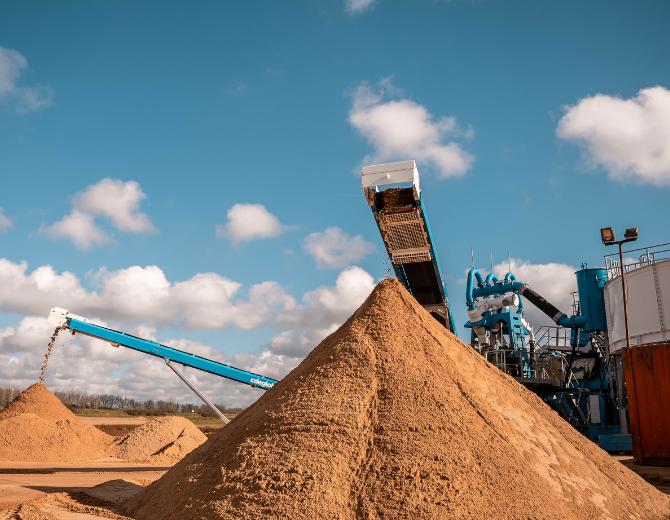
Engineered For Optimum Performance
With a deal agreed, the installation team from Molson Washing visited the site to lay out the position of the plant and to ensure services were installed correctly prior to Mick George installing the hard standing for the plant. “Having that level of service prior to the plant’s delivery was great.” Mark explained. “The installation team were always on hand to answer any questions we had during this period.”
With the pads and services installed the plant could be delivered and installed. With its modular design centred around the AggMax™ 160 scrubbing and classification plant. Designed and manufactured in Northern Ireland, the AggMax system has been designed and built to withstand years of punishing aggregate processing.
Incoming material is fed into the 13m3 hopper over a set of grizzly bars which then uses a heavy-duty Toughflex conveyor to steadily send the material out into the plant. Part way up the conveyor is an overband magnet to pull any metals out of the material to reduce potential damages and blockages further into the system. The free-flowing material is then deposited into the AggMax 163SR with an Infinity H2-60 pre-screen, where it enters the washing process. The unit is lined with TEMA Isenmann polyurethane screening media to increase the lifespan and reduce maintenance of the unit.
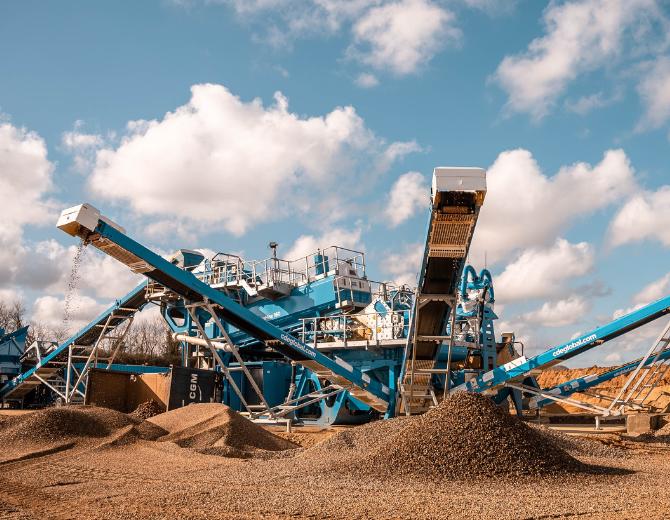
An Environmentally Friendly Solution
Material then passes into the RX160 RotoMax log washer. Another heavy-duty unit, the RotoMax uses twin-shaft design to clean the material passing through. Retention of the material can be easily controlled through the rotation speed of the shafts ensuring material is processed correctly. The unique spiral alignment of the paddles has been designed to reduce the shock of intermitting loads on the gearbox and bearings and ultimately prolong component life and reduce downtime. The outgoing material is then passed into a second, similarly sized Infinity sizing screen with any waste material picked up on an Infinity D1-43 trash screen.
With the aggregates leaving the plant via three conveyors, water containing sand is then passed through an EvoWash™ sand classification system with dewatering screen. Again, this unit is lined with polyurethane panels to reduce wear and produces both a fine and coarse grade of sand via two more conveyors.
One of the prerequisites for the plant was its ability to be environmentally friendly. “We were very surprised to find out that we only needed a 103kW power supply for the entire plant.” Mark commented. “The low power consumption and added benefit of low water requirements has meant the plant is very efficient to run.”