Tonnage
150tph
Material
C&D Waste
Output
2 Sands | 3 Sized & 2 Oversized Aggregates
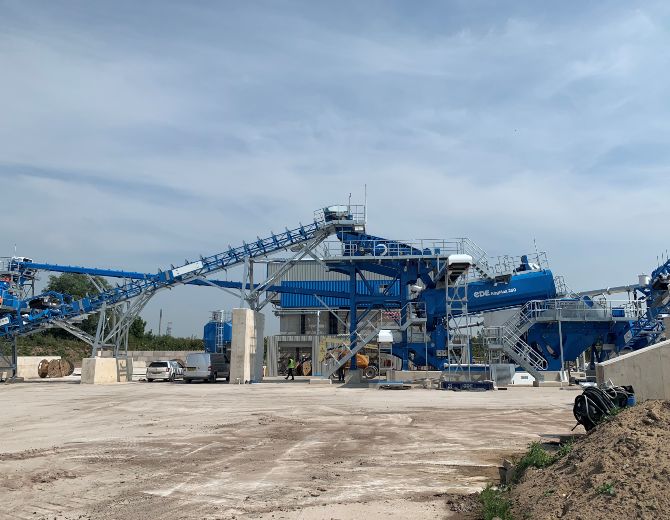
THE CHALLENGE
With over 35 years’ experience, ASH Group is committed to sustainable waste management solutions. One of the UK’s leading waste and resource management companies, its expertise spans waste management, skip hire and energy solutions, and with a new investment in a CDE wash plant it will now launch its new venture into aggregates with ASH Aggregates this September.
Based at Ellesmere Port, ASH Aggregates will begin producing washed sand and aggregates, with a core focus on sustainability for the construction industry. The new 150tph materials processing facility will maximise yields from available resources, producing up to five washed aggregates, 0-2mm up to 80mm, for resale and reuse.
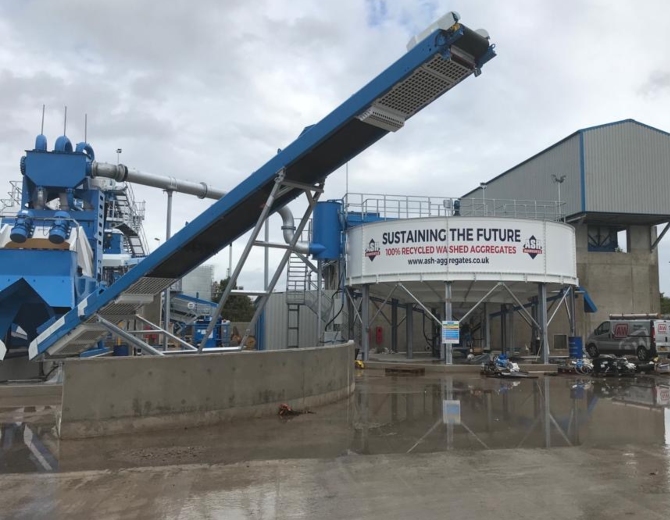
THE SOLUTION
The plant solution begins with CDE’s R4500 primary feeding system. With its scalping unit and unique design offering protection to the downstream process the R4500 machine has the capability to process some of the toughest construction and demolition waste. Following on from its aggressive screening process, the R4500 will feed the system with a controlled and constant flow of material. The machine integrates seamlessly with the AggMax 251 as part of a modular process.
The largest of the units the AggMax 251 is a scrubbing and classifying system to treat the toughest of materials. The material is first rinsed on a ProGrade screen, where all material smaller than 40mm is taken into the RotoMax, the heart of the AggMax machine. The washed oversize material is then introduced to an impact crusher before being fed back onto the main feed conveyor. The sub 40mm material is scrubbed by the RotoMax to break down the remaining clay balls, organic material that may exist in the material is removed by floatation at the rear of the RotoMax. Post RotoMax, the aggregates are screened further on a ProGrade dry screen to create three clean, sellable aggregate products: 4-10mm, 10-20mm and 20-40mm.
The -4mm particles are transferred to the EvoWash™ sand washing system for further processing and separation into two differing sizes, 0-2mm and 0-4mm. The hydrocyclone technology within the EvoWash™ ensures quality fines are recovered from silts and clays within the feed material.
Washed product outputs are stockpiled from accompanying conveyors while the silt and clay fraction flows with the waste water to the next stage of processing. Fines are passed to the AquaCycle™ A600 water treatment system which allows high rate settlement of the fine particles to the bottom of the thickener tank. The now clean water overflows the thickener tank into a water tank, ready for pumping around the plant again.
Sludge produced by the AquaCycle is then taken to a filter press which extracts the remaining water that exists within the sludge. Not only does this reduce the water requirement of the plant, the dry cake produced in some cases can be sold as another product, allowing the wash plant to become 100% efficient in terms of material produced for sale.
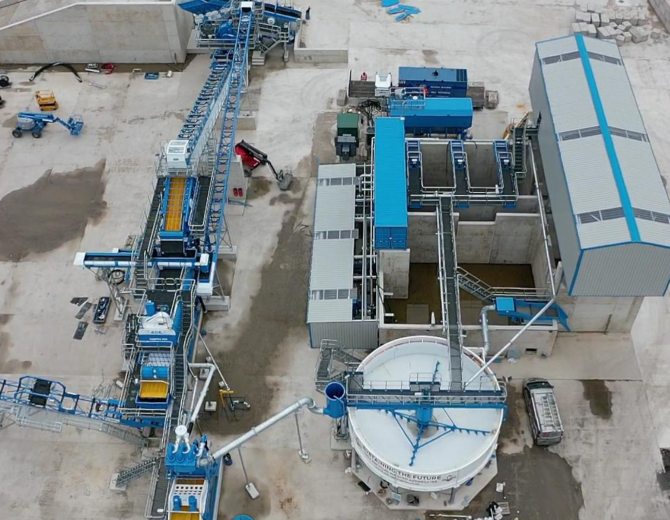
THE RESULTS
The operation will produce three sized stone aggregates and two high-quality washed sands, with two additional oversized aggregates which will help meet the needs of the surrounding area, and further afield. ASH Group and CDE began the design process in 2018 and worked together to create a unique system that will grow with the company and industry – ensuring maximum resource recovery. The 2020 launch will reduce landfill waste of C&D waste while offering employment opportunities for the local economy.