Tonnage
200tph
Material
Sand & Gravel, Quarry Waste, Limestone, Crushed Rock, Manufactured Sands
Output
2 Sands | 3 Aggregates
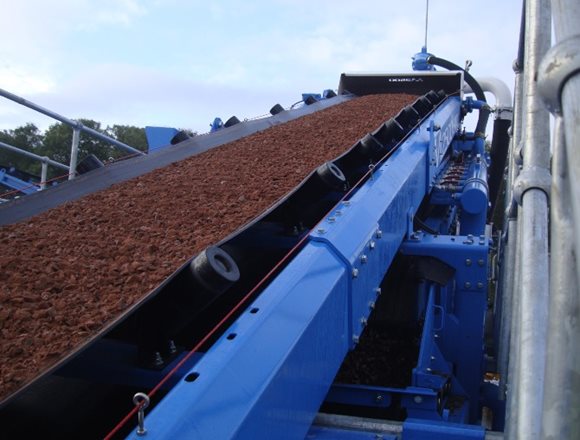
THE CHALLENGE
Prior to the installation of the CDE wash plant Grange Quarries had to buy in washed sand and aggregates to meet their supply needs for their concrete manufacturing facility.
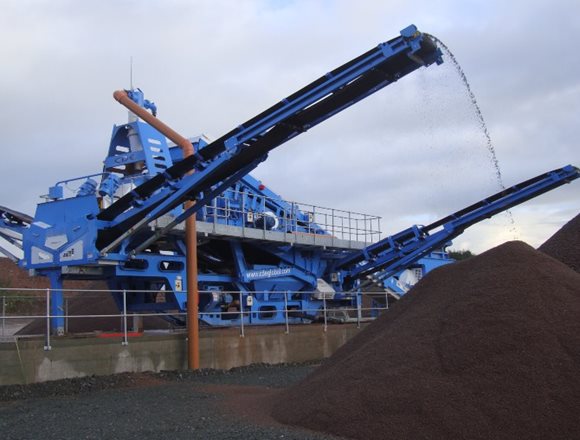
THE SOLUTION
The new plant is situated at Kelhead Quarry near Annan in Scotland and includes the M2500 E4 mobile washing plant and AggMax 83 portable logwasher. Operational since October 2012 the new plant has a capacity of 200 tonnes per hour and is processing 0-75mm limestone conglomerate material to produce a 0-4mm washed manufactured sand as well as 4-6mm grit and three washed aggregates – 6-10mm, 10-20mm and 20-40mm. The 40-75mm material is crushed and fed back to the washing plant.
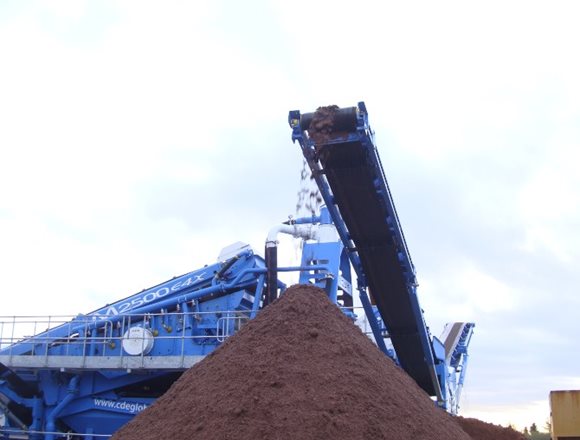
THE RESULTS
Operational since October 2012 the plant has a capacity of 200 tonnes/hr & is processing limestone to produce a manufactured sand as well as three washed aggregates
A modular washing plant has allowed Grange Quarry to increase the efficiency of their concrete manufacturing operation by eliminating the requirement to buy in washed sand and aggregates.
The efficiency gains have come from eliminating the requirement to buy in washed sand for use in the concrete plant operated by Grange Quarry at Kirkburn, Lockerbie.
The washing plant has also allowed us to enhance the quality of our concrete aggregates which has not only introduced efficiencies to our production processes but further improved the quality of our concrete products.”
It was the introduction of the AggMax system that enabled Grange Quarry to produce concrete specification aggregates from the limestone conglomerate material at Kelhead Quarry. The clay present within the feed material required an attrition system which would effectively separate the clay from the limestone aggregate material.
“We went to see the AggMax system in operation on a C&D waste recycling project for Malcolm Construction in Irvine” explains Stuart Dodd. “This demonstrated to us the capability of the machine to effectively deal with the clay in our material.”