As published in Trenchless Magazine, August 2024
In an effort to help customers minimise waste to landfill, New Zealand company InterGroup sought out the expertise of CDE Group to build a resource recovery facility fit for the job.
Based in New Zealand, InterGroup provides a wide range of infrastructure and industrial services to central and local government and private entities.
InterGroup General Manager – Business Development Sam Clive stated that a significant portion of their work involves maintenance activities, which generates a large volume of waste.
These maintenance activities present challenges when it comes to sustainable disposal, due to mixing of materials and high contamination levels.
“We’ve seen an increase in desire across the sector over the last decade, to start trying to achieve better and more sustainable outcomes.
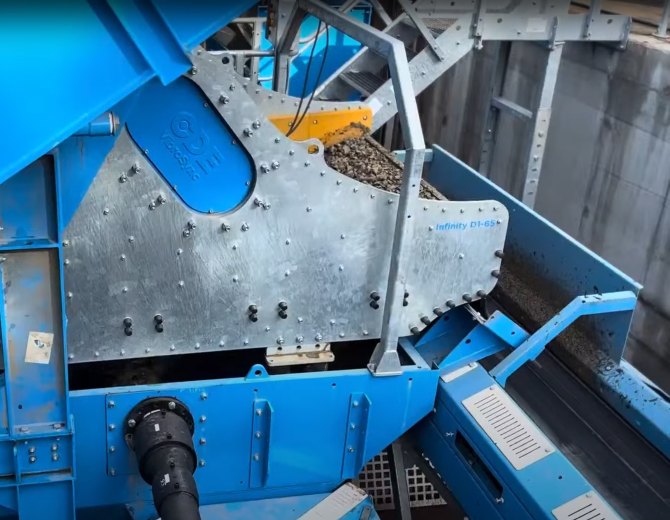
A FIRST OF ITS KIND FOR NEW ZEALAND
"One of the big pushes in New Zealand is minimising waste to landfill,” Clive said. “We’re always trying to help our clients achieve their goals and this was an area where we thought we could help. Because we’re doing all the maintenance on their infrastructure, we’re actually the ones collecting and generating a lot of that waste product.”
With the central government slowly increasing the waste levy, more and more companies are incentivised to start investing in technology that can divert waste to landfill. For InterGroup, a new resource recovery facility was one way to achieve this for clients, with the introduction of their wet processing plant.
“We came across CDE Group’s products and with the volumes of waste we were bringing through our facility, and the type of waste, we saw that we could substantially decrease the amount of waste that’s going to landfill,”
Clive said. “It’s a double benefit where we get this great sustainable outcome of reducing waste to landfill, while we’re also saving money for our clients and being more competitive at the same time.”
Based at InterGroup’s Auckland depot, the resource recovery facility has a range of innovative technologies from CDE including a HYDRO:TIP™ solid/liquid tipping system, an AquaCycle™ thickener water cleaning and treatment system, and an AggMax™ scrubbing and classification system.
CDE Australasia General Manager Daniel Webber noted the facility is the first of its kind in New Zealand and incorporates several innovative elements.
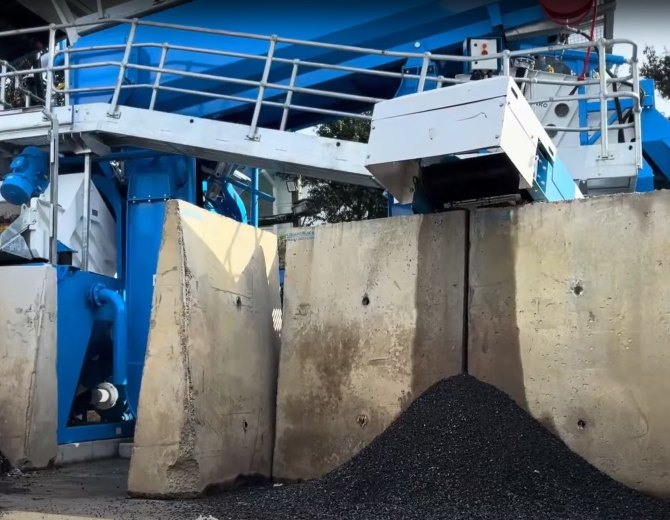
Engineered To Reduce Waste Disposal Costs
One example is the HYDRO:TIP which effectively dewaters and grades hydro excavation and non-destructive digging waste. This process reduces the volume of material sent to landfill, and therefore disposal costs.
“It’s the first time a HYDRO:TIP has been installed in New Zealand and the speciality of that machine is that it’s a directive system,” Webber said. “The HYDRO:TIP is placed into the ground for direct feed of material from tankers, resulting in quick and easy offloading for maximum efficiency and minimum downtime, allowing tankers to get back on the road faster.
“It has the added advantage of being the safest method.” The AquaCycle primary stage water treatment handles the responsibility of ensuring up to 95% of the processed water is recycled for immediate recirculation. For InterGroup, it was these innovative solutions from CDE that cemented their choice for the resource recovery facility.
“We wanted to build a facility that was going to have not just an impact on InterGroup’s business, but an impact on our region,” Clive said. He also noted CDE’s track record as a contributing factor. “CDE has a long history in building wet waste processing plants and a really strong track record,” Clive said. “They gave us the confidence that they will be able to deliver and build a facility that would meet those goals.”
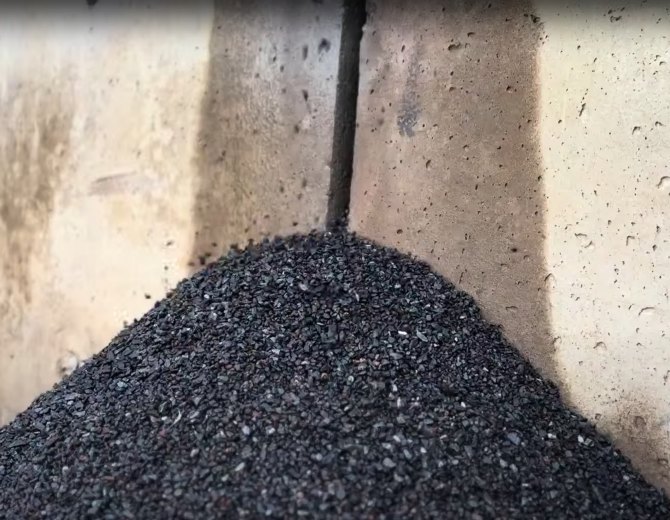
Engineered For Zero Waste
CDE also offers extensive support across all stages of the project, according to Webber. “For installation and commissioning, it’s boots on the ground,” Webber said. “The last thing a customer wants is a different face on their project every week. We had a core project team, and the customer knew their point of contact.”
Now, with the facility open, the training wheels are off, with the two companies discussing support with the spare parts profile. “We’ve got close to $2 million worth of parts sitting in southeast Queensland, so a lot of those can be on site the following day on an air freight option” he said.
Clive commended the support from CDE and the team. “I met the guys out on site, and they are very helpful and very passionate people,” he said. “We’re a very passionate company so, it’s nice to work with a company where the employees share an equal level of enthusiasm.”
Now that the resource recovery facility has officially opened, Clive said initial results have been positive. “The first day, we ran it for seven hours. We put a substantial volume through, and it worked really well,” he said.
So far, none of the recycled product has had to go to landfill.
Clive added that the company is still refining their output material, but are in the process of talking to suppliers who can purchase the clean aggregates and sand.
“I really like the idea of a circular economy model and sustainability lifecycle, so I’d love the product to go back to the people or back to the kind of clients that produced it,” he said.
“The companies that are doing hydro excavation works or utilities repair, it’d be awesome to get that product back into those markets.”
Webber commended InterGroup for bringing this kind of facility to the New Zealand market and noted the opportunities to come.
“A lot of government organisations are looking at responsible sourcing,” Webber said. “So how are their contractors handling the material that they’re being the custodians for?
This certainly ticks all those boxes. “It should really kickstart that circular economy discussion and InterGroup has certainly set the benchmark.”