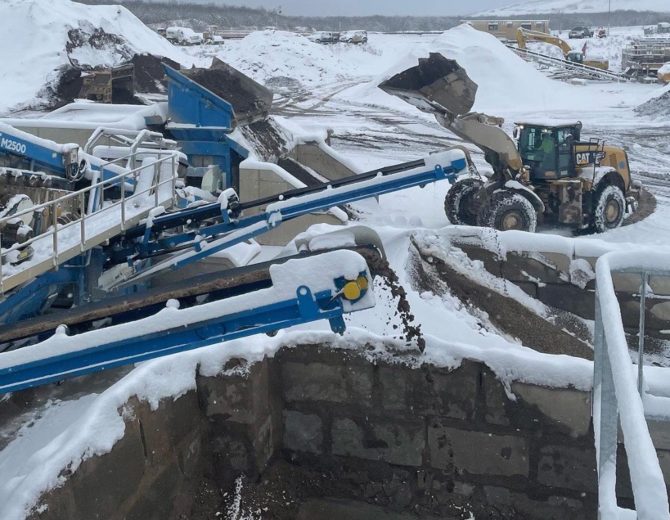
SAFEGAURD YOUR PLANT FROM THE COLD
The icy grip of the winter season presents a unique set of challenges for wash plant operators, but with effective planning materials producers can protect their investment and ensure their operations are ready for an efficient return to production in spring.
When it comes to plant maintenance, it is essential that any potential complication is identified and remedied quickly to protect an operator’s investment and ensure optimal performance, particularly during the coldest months of the year when washing and classifying equipment is especially susceptible to the elements.
“In this business, time is money,” explains Mike Matusik, a customer relationship manager at CDE.
“Implementing a robust maintenance programme year-round will safeguard equipment from the taxing cold weather, helping to minimize downtime for unscheduled maintenance and maximize product output.
“With planning and preparedness, operators can ensure the safe and efficient shutdown of a wash plant in winter and facilitate an efficient restart of operations in the spring. While there is no one-size-fits-all approach, there are some basic steps operators can take to protect their investment.”
here are our TOP TIPS for wash plant operators during the cold months:
- Water Management: Effective water management as the cold weather sets in should be paramount for operators. It’s advisable to drain all standing water from tanks and pumps when plants are mothballed for the winter season otherwise you risk lines freezing, cracking, and leading to a delayed and costly restart in the spring.
- Insulate: The winter months can bring unforgiving conditions, so consider insulation to protect pipes, valves and pumps. Ensure your control cabin has been closed and, if possible, keep the internal heating on to protect the beating heart of your plant from plummeting temperatures.
- Tip Three: In addition to draining the system and, where possible, insulating pipes valves and pumps, it’s also advisable to keep valves open during winter shutdown as this will prevent any residual water accumulating in the system.
- Tip Four: Clean out spray bar nozzle heads and ensure smaller pipework is free of debris such as silt and sands. Ensure your spraybars are receiving adequate water pressure, and the spray from the nozzles are fanning at the correct angle. This will allow you to get more water on to the screen to ensure the product is getting the best washing treatment.
- Safety Protocols: Winter also poses additional safety concerns for plant operators. Consider refreshing and rehearsing your training procedures to ensure your teams are well versed in the appropriate safety protocols when working in the vicinity of a wash plant to avoid slips, trips, and falls.
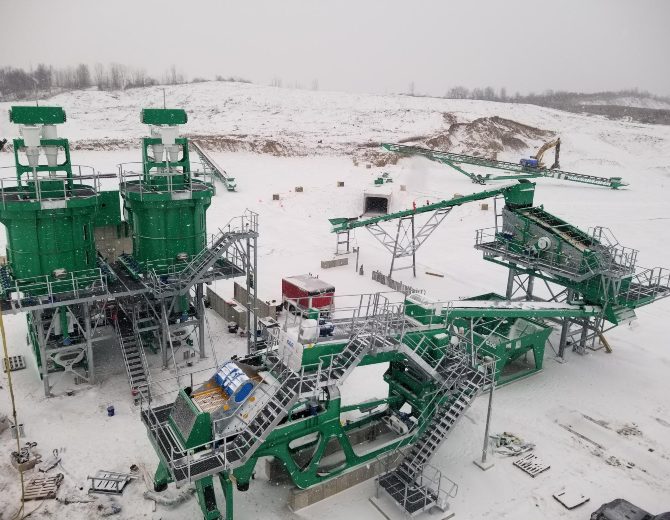
PREVENTION IS KEY
In order to respond in a timely manner, we hold stock of common parts locally, from screen media and cyclone parts to marsh mellow springs, motors, and gearboxes. These are all available for immediate dispatch to customers from our North American headquarters in Fort Worth, Texas
“Our CustomCare team holds a complete order history detailing critical plant components and spare parts for each of our customers’ wash plants. This helps ensure straightforward re-ordering and allows our service engineers to maintain a comprehensive overview of how a plant is performing.”
Prevention is always the number one focus, Bunting adds.
“We work closely with our customers to deliver regular preventative maintenance inspections which are highly effective at identifying potential issues before they arise and adversely impact production. Our plant health checks are just one part of our commitment to providing a lifetime of care to customers and ensuring their long-term success.”
As part of our free plant health check initiative, our expert service engineers will analyze the plant’s condition, highlight signs of wear or irregular noises, identify parts in need of replacing, schedule regular maintenance, support and advise operators, and recommend fast-moving parts ideal for storage on site.