Sand, after water, is our most used natural resource. We are living through a global sand crisis, whereby the consumption of sand, for use in everything from construction to computers, has seen demand outstrip supply putting increased pressure on natural resources. It’s a finite resource that is rapidly depleting. It is estimated we use 50 billion tonnes of sand each year, and this figure is expected to continue rising.
It is fundamental to maximise sand recovery from existing supplies and use natural sands only when necessary to ensure we manage the world’s resources sustainably.
Around the world, millions of tonnes of sand are destined for use in lower value concrete due to naturally occurring contaminants such as lignite.
In this issue of our Innovation Series, Darren Eastwood, Business Development Director and John Quigg, Senior Technical Engineer, look at how our engineers have adapted contaminate removal technology to reach previously unattainable levels of lignite removal, maximising the value of the sand for use in higher value outputs.
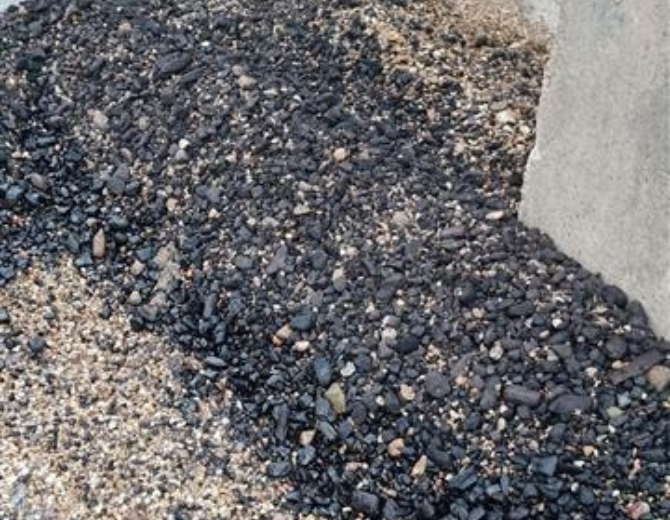
Let's Start With The Problem
Lignite is a soft, black, or brown coal-like substance and can be present in localised sand and aggregate deposits all around the world. Considered a contaminate in the sand and aggregate industries, it can have 2 detrimental effects if it makes its way into concrete production:
1. Staining
When finishing concrete, the lighter, softer lignite fraction rises to the surface and as the concrete hardens, the lignite becomes visible as dark smears. The severity of this depends on the quantity of lignite in the material and its impact is determined by how visible it is in the finished concrete. The detrimental effect ranges from minor blemishes to major discolouration.
If staining occurs in concrete that’s not visible, such as foundations, it’s not a major problem. However, it’s not something you want to see on a visible concrete wall, major infrastructure, or products such as paving. It doesn’t look good or instil confidence in the structure.
2. Popping
While smearing is unsightly, ‘popping’ is an even more problematic issue. Popping occurs when the lighter lignite rises to the top of power trowelled slabs and architectural finishes. The lignite particles expand and explode out of the concrete. This leaves holes which can vary in size. It can have a detrimental effect on the concrete’s integrity, leave an uneven finish, impact its wear and lead to challenges with finishes. Again, it doesn’t instil confidence in the structure.
As a result, international standards for acceptable limits of lignite content in sand and aggregate for concrete production are very strict and contaminated deposits will be rejected.
Depending on the end use of the concrete, the permissible lignite level in the sand can vary. The USA, and some other countries such as Thailand, follow the ASTM C33 specification for concrete. This standard allows 0.5% lignite in the sand if the concrete surface is important. For all other concrete, 1% is the maximum content allowed.
In the UK and Europe, the EN 12620 standard permits 0.5% lignite to be present in the sand. However, if the concrete surface is important, the lignite limit decreases to 0.25%.
Some producers simply accept that their deposit has lignite and use it as it is or sell it for use in lower value products while others have sought solutions to remove it.
So how do sand and aggregate producers remove lignite in order to maximise the potential of their deposit and eliminate waste?
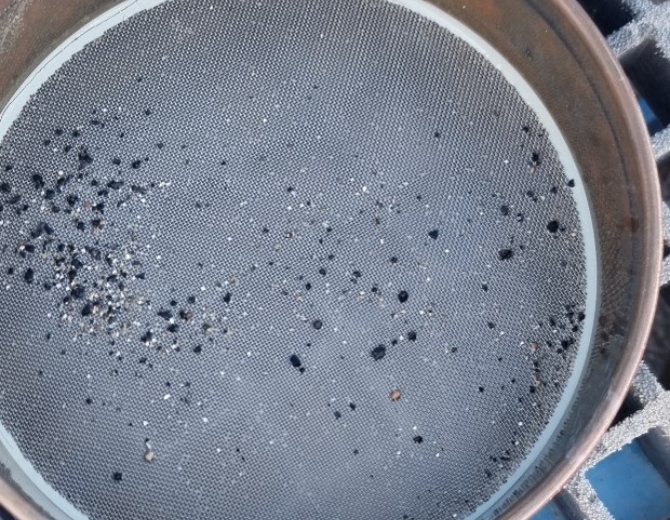
The Traditional Solution
To remove lignite from sand and aggregates, operators have traditionally used sand screws.
Based on water screw technology that’s been around for millennia, sand screws work by agitating the sand in water to float organics or other light weight contaminants over a weir. It utilises upward flow to generate a density separation – the lighter material floats, the heavier material sinks. As lignite is lighter than the sand fraction, it should float off. The heavier sand fractions sink to the bottom of the sump and are drawn out for further processing by the rotating screw.
The problem with this solution is that cut points are inaccurate, making it difficult to consistently produce in-specification sand. While most of the lignite fraction will float off, not all of it does. Typically, friction is required to separate the sand and lignite. The material movement on its own cannot produce enough impact to achieve this. Multiple passes through the screw can help but this only marginally improves the result while adding more time to the process and increasing costs.
In recent years, as sand and aggregate producers take on board the part they can play in sustainable production, we have seen an increase in requests to remove lignite and other contaminants in order to improve the material quality and maximise the commercial return. Customers are embracing sustainable production as they understand there is no alternative.
Elevating standards – The 0.1% challenge.
We have recently completed a project with a concrete producer in the US that has high quantities of lignite spread throughout their sand and aggregate deposit. Their previous operation used the sand screw method and continually failed C33 specification.
This customer wanted to raise the bar on sand production quality. No longer happy with using their precious deposit for lower value outputs, they wanted to supply a broader customer base that demanded higher quality products.
Rather than just meeting C33 spec requirements of 1% lignite, they challenged us to design a solution that would guarantee 0.1%. That is 10 times less than C33 spec allows but would enable them to produce a higher quality, more consistent product that they could sell into new markets for higher prices.
-La-Chola-plant-overview-670x520.jpg)
This was a 3-part challenge.
1. Remove lignite from the sand fraction to surpass C33 specification - Target 0.1%
2. Classify the sand from a very inconsistent feed to meet C33 size specification.
3. Remove lignite from the aggregate to enable its use in concrete.
During the design stage of this project, we worked closely with the customer to analyse their material and the data they had accumulated from their previous operation. We conducted laboratory tests and had numerous onsite visits to understand the capabilities of our equipment to ensure we could deliver the standards the customer needed to achieve. We utilised our experience and data from other lignite removal projects to determine the most productive and efficient method to achieve the customers objectives.
A DIFFERENT APPROACH
1. Lignite removal
We deploy a number of different plant items within our range to wash and classify material and typically use our Counter Flow Classification Unit (CFCU) for contaminant removal. The CFCU separates material based on density, and sizes material, in one process.
The CFCU uses counter flow forces, (also known as upward flow) in a chamber to classify material by gravity. Water is used to suspend sand particles and the high density in the chamber provides a boundary through which the lignite cannot pass. The density of the fluidised sand bed can be controlled at a set cut point allowing the heavier sand fractions to sink through this bed to the bottom of the chamber, while the lighter lignite floats out the top, giving us a controlled density separation.
We knew we could remove most of the lignite with the CFCU while retaining the fine sand, resulting in a higher sand yield. The challenge for us in this case is to set and maintain this specific density to maximise the removal and reach this ambitious target.
2. Sand Removal
The second part of the challenge was to design a solution that processed the fluctuating feed material. The fraction size in the raw feed fluctuated +/- 40% between the maximum and minimum sieve sizes.
These fluctuations test both the capability of the equipment and the complex control logic of our systems to ensure consistent and reliable production.
For the removal of lignite, our aim was to use the CFCU to maintain a stable material bed with a bed density that is higher than that of the lignite we are removing. In this case we aimed for a bed density at the overflow weir which matched that of lignite which has a specific gravity of 1.3. In comparison, sand has a specific gravity twice that of lignite at 2.65.
The CFCU maintains the bed density through a control loop and as such can prevent the short circuiting of lignite through the tank. This unit was specially designed with a secondary density control system which could measure the density at the bottom of the tank. This gave us the ability to control the underflow to a desired specific gravity and reach the C33 sized sand specification.
3. Aggregates
The third aspect of this challenge was to remove the lignite contamination from the aggregate to enable the customer to also use it in concrete production.
Our RotoMax™ log washer is normally deployed to provide the scrubbing required to remove clay and contaminates from aggregates. Synchronised shafts with scrubbing paddles in a spiral formation move the fluidised aggregates through an inclined sump, scrubbing the material and removing contaminants.
As the agitation liberates the material, the upward flow enables the lighter lignite to be removed in a controlled fashion. As a result of material testing our engineers determined additional upward flow was needed and set about designing a solution that increased the volume and depth of water in the tank.
This extended the retention time in the water, increasing the effectiveness of the density separation inside the log washer to maximise lignite removal and achieve the customers targets.
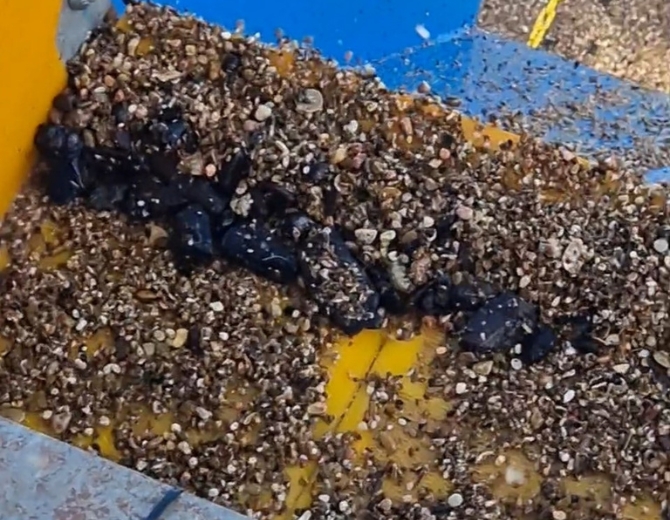
The Outcome
Based on our material testing and data from previous installations, the CFCU was setup and configured to very precise specifications. When the test results of the first material came through some further minor refinement was necessary to optimise the yield to C33 specification.
The finished sand product was deslimed to a higher level than the customer anticipated, achieving the sand equivalency of 99, well in excess of ASTM specification of 85.
With the aggregates, the immediate success of the system was evident with lignite and coal 5 - 10cm / 2” - 4” in size being removed efficiently with minimal loss of product. The RotoMax solution produced a clean aggregate ready for use in concrete production.
Additional benefits
While the objective was to improve the product quality for the customer, other benefits were realised that improve the projects long-term sustainability. This new system can process higher volumes of material than the old screw, so production capacity has been dramatically increased, and efficiency improved. By eliminating rewashing and double handling labour costs have been reduced. This more robust solution enables the plant to operate double shifts with minimal downtime for maintenance.
We aim to maximise the recovery of every grain of sand, enabling customers to realise the full commercial potential of their materials. Through removing lignite and other contaminants we can improve sand quality, minimise waste and extend the life span of marginal operations. This in turn reduces the impact on virgin materials.