Tonnage
150tph
Material
Sand & Gravel
Output
10mm & 20mm Aggregates | Concrete Sand | Washed Oversize
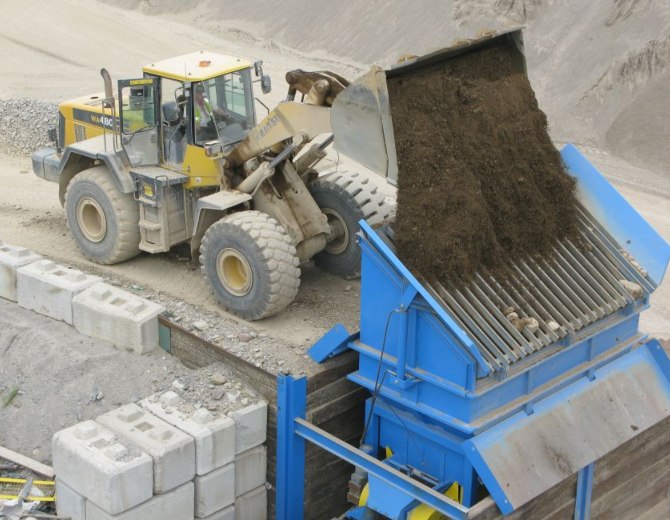
THE CHALLENGE
John A Woods is a major supplier of stone, ready-mixed concrete, concrete products and bituminous materials to the building and construction industries in the south of Ireland. It is also one of the oldest quarry firms in the region; although incorporated in 1951, the company dates back to 1914 and was the first to set up a gravel washing plant in Ireland. Its founder, John A Woods, was also a founding member of Roadstone.
The company operates in 15 locations throughout Ireland, and it was the Watergrasshill, Co. Cork site that a CDE solution was deployed to improve operational efficiencies.
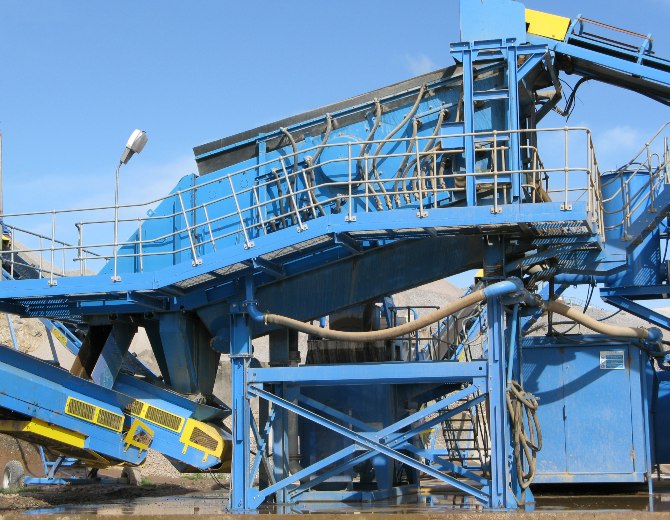
THE SOLUTION
The CDE solution incorporates a ProGrade rinsing screen, EvoWashTM washing, classification and dewatering system and an AquaCycleTM thickener, for better water management.
Material is loaded directly into a 20 tonne reception hopper. This feeds a conveyor which carries the raw material to a triple-deck 1.5m x 5.0m ProGrade rinsing screen and discharges on to it via a rubber-lined washing box, which adds water to the material to create a slurry.
Equipped as standard with abrasion resistant rubber lining on all surfaces that come into direct contact with the raw material, the ProGrade unit is fitted with rubber mats on the top two decks and polyurethane media on the bottom deck, which is standard practice throughout the ProGrade range. The feed material is washed and sized with the oversize, 20mm and 10mm products being sent down rubber-lined chutes to stockpile via mobile conveyors.
The sand is fed using gravity directly into the sump of an EvoWash compact sand washing plant, which CDE tailored to the site specific application. From here the material is pumped, via a Warman pump, to a cyclone which accurately separates the material at the customer’s required cut point (75μm in this particular case) with no unwanted fines loss.
From the cyclone the washed sand is sent to a high-frequency dewatering screen where it is dried to approximately 12% moisture content. The screen is fitted with wear-resistant polyurethane panels and features marshmallow springs for maximum efficiency. From here the dewatered sand is sent to stockpile via another mobile conveyor.
Meanwhile, the –75μm material separated by the cyclone is sent directly to the AquaCycle thickener. As the slurry enters the thickener tank, the material is mixed with a polyelectrolyte, prepared in an adjacent fully automatic dosing station, causing a thick sludge to rapidly settle to the bottom of the tank. Meanwhile, the clean water overflow from the thickener tank is sent to a storage tank from where it is pumped back to the ProGrade rinsing screen.
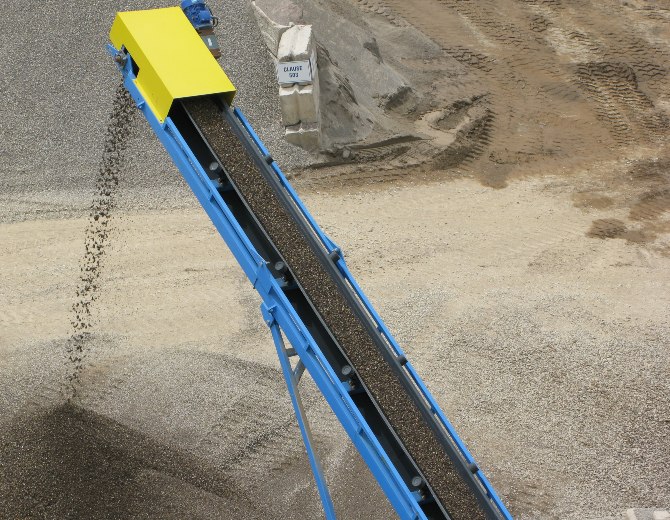
THE RESULTS
The washing plant processes 150 tph of ‘as dug’ material to produce a washed oversize, 20mm, 10mm and concrete sand. While the AquaCycle thickener enables John A Woods to recycle up to 80% of the water used during the washing process, significantly reducing the site’s fresh water requirements.
The washed sand and aggregates are used for concrete production, while the waste sludge (approximately 600g/litre concentration) is pumped to a silt pond.
This project was delivered as a contract washing partnership with CDE maintaining the plant on behalf of John A Woods. CDE’s team regularly visit site to carry out preventative maintenance inspections to ensure operational efficiencies and maximum uptime.