Tonnage
110tph
Material
C&D Waste, Crushed Concrete
Output
1 Sand (-5mm) | 2 Aggregates (5-10mm, 10-20mm)
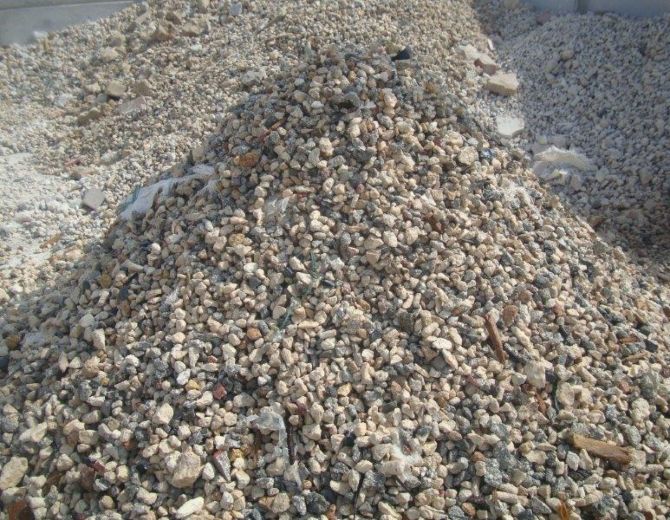
THE CHALLENGE
Located on the island of Aruba, off the coast of Venezuela, ATCO Concrete Products have taken ownership of a turnkey C&D waste recycling plant from CDE to process construction and demolition waste for use in concrete production. The ever-increasing demand for construction materials on the island of Aruba led to a dramatic increase in production and thus ATCO had to become more efficient than ever. ATCO took the opportunity to set up the first ready mix facility on the island, supplying a large proportion of the market. The addition of the washing plant from CDE paved the way for future growth for the company.
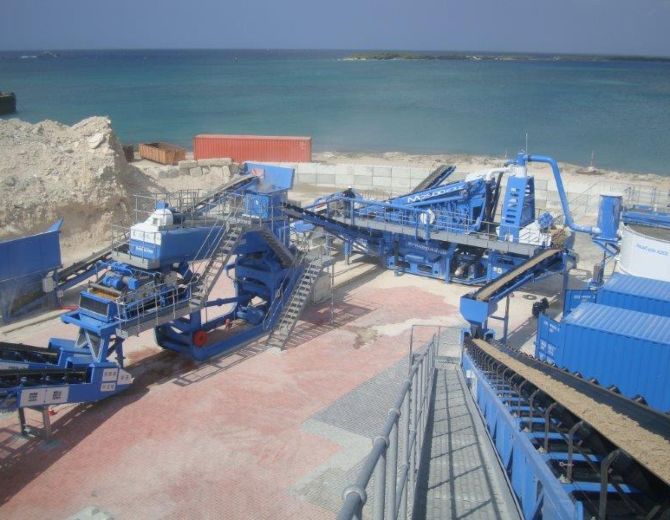
THE SOLUTION
The modular Construction & Demolition waste recycling plant onsite is comprised of an M2500 E3, an AggMax 82R, a RotoMax RX80 an AquaCycle A200, a GHT Overhead Beam Filter Press and 3 stockpile conveyors processing a variety of raw feed material up to a rate of 110tph.
The CDE waste recycling wash plant at ATCO includes a number of treatment phases including the initial feeding system, the attrition phase which scrubs the aggregate product and removes un-wanted contaminants, the aggregate screening and stockpiling system, a sand washing phase which produces one washed recycled sand product, a primary stage water treatment phase and a sludge management system. The raw feed material is delivered to the M2500 via an R15 feed hopper and tipping grid at a maximum rate of 100tph which is fitted with a 150mm screening grid.
The integrated belt feeder then transfers the material directly onto an inclined transfer conveyor which features an integrated overband magnet for the effective removal of any ferrous material which can then be discharged into an underlying skip.
On the top deck of the AggMax sizing screen, the material is passed directly through to a double deck rinsing screen featuring polyurethane matts. The top deck aperture is 10-20mm with the bottom deck aperture being 5-10mm. The 10-20mm material is fed onto a side conveyor and stockpiled while the 5-10mm material is sent to another side conveyor for stockpiling. All other material will fall through to the sump and is then pumped back to the M2500 to ensure maximum sand recovery.
Water Treatment is also one of the main stages of the process involving the AquaCycle high-rate thickener system, the wastewater from the processing plant is sent to the A200 to be recycled and reused in the process.
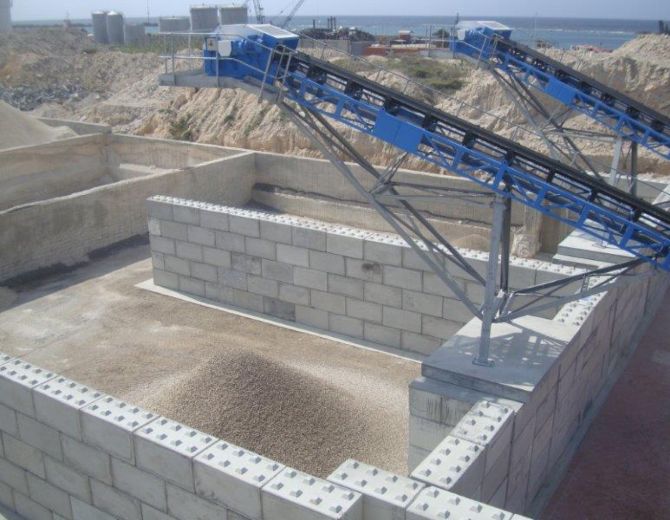
THE RESULTS
The addition of the custom C&D washing plant from CDE enabled the company to grow and increase efficiencies with the production of 2 no. washed recycled aggregates (5-10mm, 10-20mm) and 1 no. washed recycled sand at -5 mm that are being used for concrete production.
Project Management
With the remote location of the ATCO site, on-going support was a key issue for consideration at the outset of the project. The CDE Project Manager ‘ProMan’, allowed ATCO to be closely involved from the initial design stage, through to manufacturing, logistics, installation, commissioning and beyond. Project Manager Brian McCullough explained: “With all projects that we deliver, internally within the company, we appoint a dedicated Single Point of Contact for our customer which allows them to have continuous contact throughout the entire duration of project delivery. The ProMan system enabled us to communicate regularly and effectively with ATCO and they were assured that the plant would meet the specifications agreed”.